【2020 Solutions】 RelaJet Envisions the Future to Aid Hearing-Impaired with Easy 'Listen & Speak'
For the hearing-impaired, being able to enjoy a low-noise, good listening experience at a relatively affordable price is perhaps the greatest happiness in life. Chen Bai-ru, the founder of Future Insight Tech and a hearing-impaired individual, 'heard' the voices of the hearing-impaired. Understanding the struggles of not being able to hear clearly, he utilized AI technology to develop a 'Multi-person Voice Separation Engine' to help solve their challenges.
The Opportunity to Hear Again
According to statistics, there are about 99,535 people with hearing disabilities in Taiwan, accounting for about 10% of those with disabilities. These nearly 100,000 hearing-impaired individuals live in a world where 'listening and speaking freely' is challenging.
For the hearing-impaired, the two main problems faced are:
One, hearing aids are expensive; among the six major global brands, the average price is around NT$60,000, with high-end models even reaching NT$150,000, which is not feasible for an average middle-class family;
Two, the performance of traditional hearing aids is not sufficient; when the surrounding environment is too noisy or the volume too high, it becomes very difficult to clearly hear the speaker's voice.
Due to their size, conventional noise cancellation methods involving several microphones cannot be used in typical Bluetooth headsets. In noisy environments with many people talking, such as restaurants, gyms, and supermarkets, the quality of noise reduction during calls is not ideal.
Therefore, Chen Bai-ru, also a hearing-impaired individual and the founder of Future Insight Tech, uses AI deep learning technology to achieve noise removal and output clean human voices with just a single microphone.
Feature Recognition Completed in 10 Milliseconds with No Latency in Speaking and Hearing
Being able to complete all feature recognition calculations within 10 milliseconds is the greatest advantage of the RelaJet Multi-person Voice Separation Engine. Why 10 milliseconds? Because if the processing time for speech by hearing aids exceeds this limit, it can lead to a delay that causes dizziness in the individual. Therefore, any hearing aids classified as medical devices are required to complete all processing steps within 10 milliseconds.
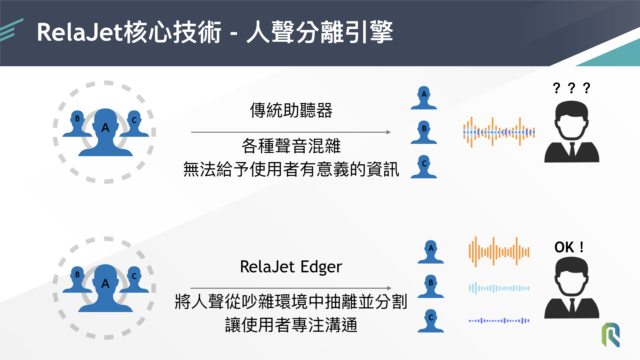
The US Food and Drug Administration (FDA) is set to allow the sale of non-prescription (Over-the-Counter, OTC) hearing aids in 2020, which will significantly reduce the costs of experimentation and certification and make hearing aids more affordable. Additionally, the purchasing channels will be more open, eliminating the cumbersome fitting process. Future Insight is seizing this business opportunity, actively establishing partnerships with the top six global hearing aid brands, and also entering the Bluetooth headset market to benefit more hearing-impaired individuals.
Future Insight Tech's specific approach to incorporating AI involves a customized model with an algorithm chip, achieving a noise reduction of 20Db and power consumption below 9Ma. This noise reduction model requires only a single microphone to remove noise and output clean human voices, significantly enhancing the call quality of Bluetooth headsets.
「Translated content is generated by ChatGPT and is for reference only. Translation date:2024-05-19」