【2020 Solutions】 Riding the AI train, Shinewave forms an alliance with ASUS to tackle smart manufacturing

After the outbreak of COVID-19, the global manufacturing supply chain has undergone major changes, and the demand for localized production has greatly increased. To help traditional industries achieve digital transformation and enhance their competitiveness, Shinewave, which has more than 20 years of software experience, has also been actively branching out from information technology (IT) into operational technology (OT) in recent years, and has jumped on the AI train, working with its parent company ASUS to seize the smart manufacturing market.
Software expert Shinewave transforms into a solution provider
Shinewave is a software subsidiary of ASUS. It was established in October 1998 by the product business group team of the Institute for Information Industry (III). "The company's slogan was 'We deliver quality software' during early periods, but it has now been adjusted to 'We deliver quality solutions.'" Chun-Hua You, President of Shinewave, added that Shinewave has also transformed from providing software products to providing total solutions in response to customer needs. The solutions provided include software, hardware, and system integration. With more than 20 years of experience in manufacturing, Shinewave is now be able to create higher value for customers with the support of AI and IoT.
The main purpose of Shinewave's "Manufacturing Factory Automation Information Management System" is to help manufacturing customers strengthen the collection of production data in various units of the factory (such as materials, production management, manufacturing, quality control, and warehouse management), and to quickly and accurately determine the current condition of production. The complete network mechanism allows remote decision-making and factory management to be synchronized, and effectively monitors the manufacturing, quality control, and shipping processes, monitoring production in real time and improving product yields. This achieves production efficiency and customer satisfaction, and reduces unnecessary management costs that do not add any value.
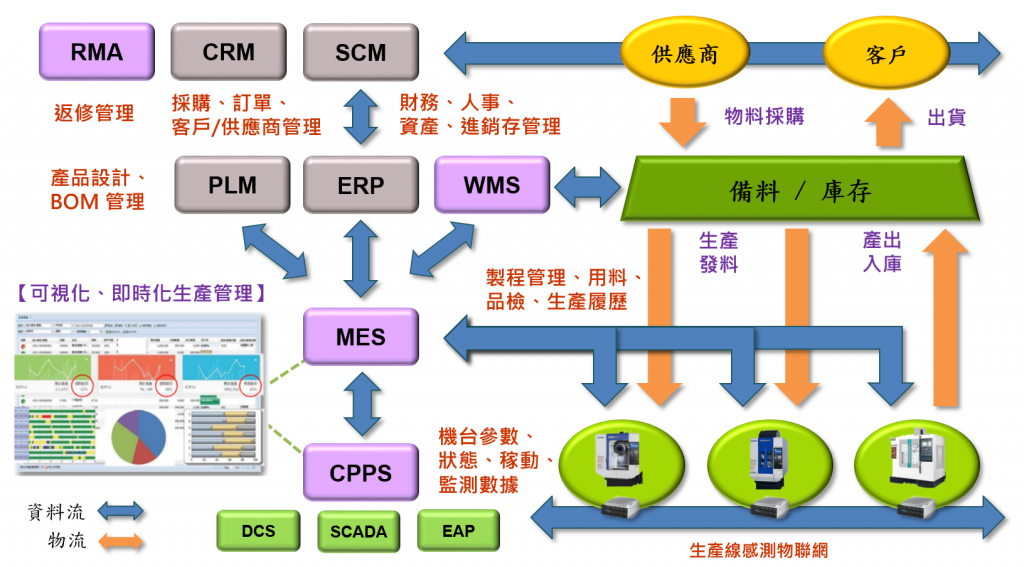
▲Shinewave helps customers create a blueprint for smart manufacturing with its complete information system framework and solutions
Shinewave is committed to developing total software solutions for factory automation in the manufacturing industry, and has accumulated experience in more than 200 factories so far. Its customer base covers 3C product assembly, notebooks, and industrial computers, and has a leading position in relevant markets. Besides building strong competitiveness in the electronic and IT product assembly industry, Shinewave also assists corporate customers with widening their lead in the industry, and continues to strengthen data collection from each unit of the production line, allowing remote decision-making and on-site management to be synchronized in real time, while reducing factory management and maintenance costs. In terms of future business expansion, traditional industries that are highly dependent on machinery have strong demand for information, visualization and AI. This is the industry that Shinewave is currently actively focusing its efforts in.
Implementation of traceability to enhance the competitiveness of the design process
"Wide variety in small quantities and customized markets are an important driving force of smart manufacturing" said Chun-Hua You. In the past, foreign companies including HP, IBM, and Dell required Taiwanese foundries to establish a complete "traceability" system. The electronics assembly industry is highly labor-intensive, has limited machine control capabilities, and has a large amount of production and testing data. The key to competitiveness lies in the collection of data through information systems and providing traceability and analysis capabilities, so that OEMs can design products, improve quality, and improve processes.
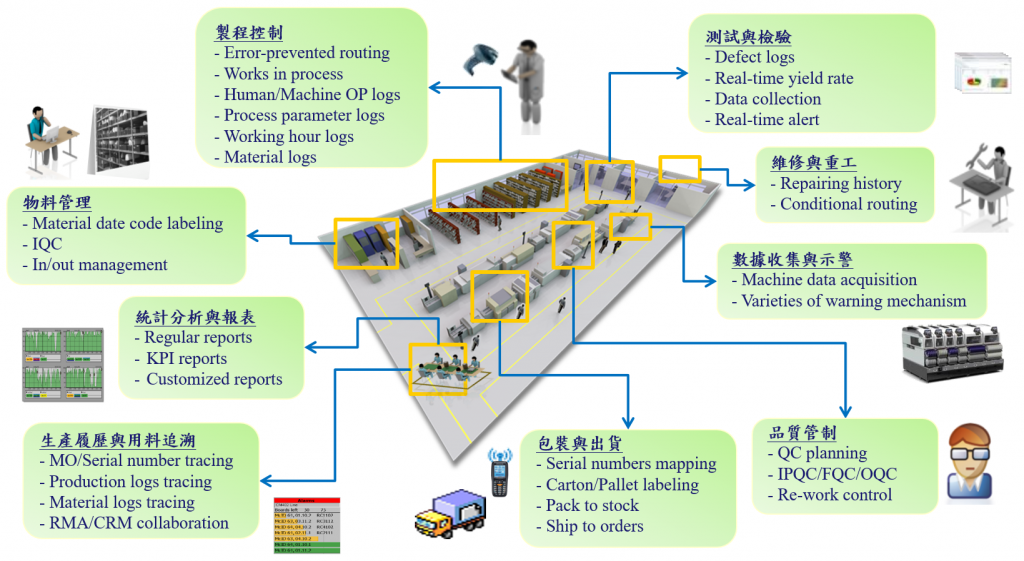
▲Shinewave provides total solutions for electronic assembly plants
In addition, data collection is also widely used in testing and quality inspection. Using burn-in operation in the electronics industry as an example, the system automatically downloads and executes the test program by comparing the machine model and material number, monitoring abnormal conditions in real time, adjusting the test environment or suspending operations at any time. The product quality can be immediately determined without waiting for the end of the testing process, which also allows companies to reduce labor and time costs.
Shinewave has accumulated a wealth of experience in electronic assembly processes. Chun-Hua You pointed out that the consumer electronics industry adopted information systems earlier, and the main production lines are already in the Industry 3.0 stage. To achieve the goal of Industry 4.0, future efforts will be directed to AI+IoT. In terms of AI, Shinewave is actively working with its parent company ASUS in AI image processing, recognition, and defect detection, and expands and deepens AI technology application solutions. In terms of IoT, Shinewave has cooperated with a number of manufacturers in connecting machinery to the Internet and data acquisition, helping customers monitor the status of on-site production equipment in real time, reducing losses caused by abnormalities.
Over the years, Shinewave has combined its experience with major ERP companies in the industry to provide customers with total solutions for information collection at the internal planning and execution levels within the company. Now it hopes to use its own capabilities to further integrate AI and IoT, join forces to provide customers with total solutions, and assist manufacturers with building a core information flow system for smart manufacturing through Shinewave's MES, integrating ERP, PLM, APS, and WMS and combining it with the physical layer of equipment automation. This will allow vertical and horizontal information to be completely collected and actively used to develop smart factories and move into flexible smart production.
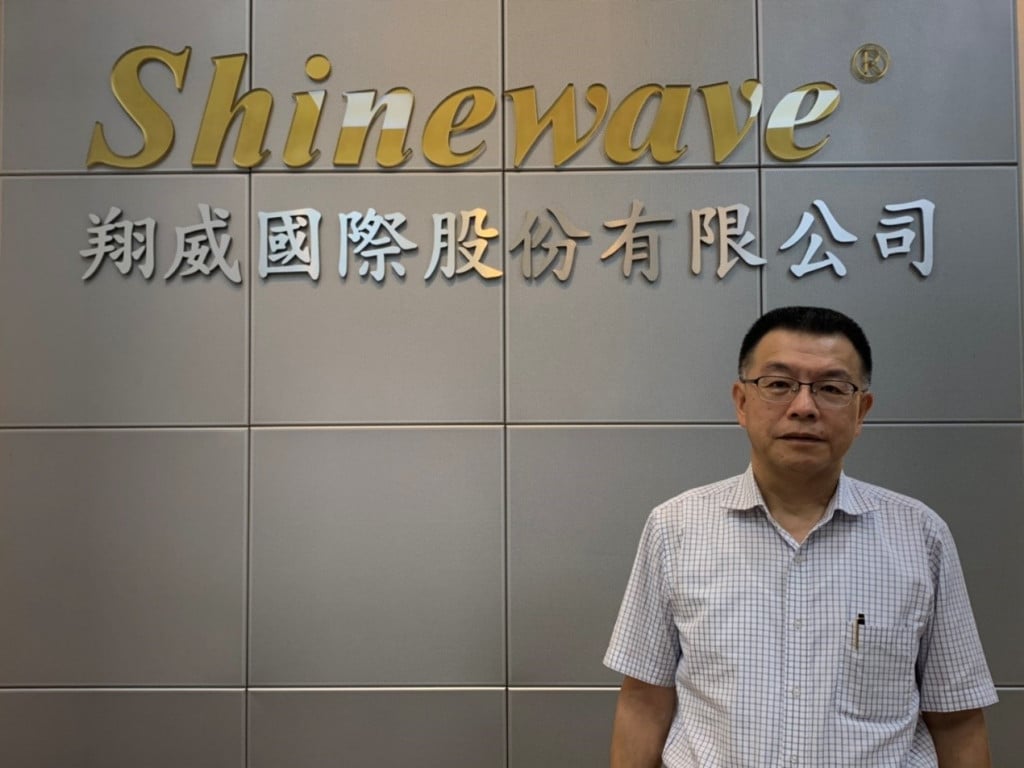
▲Chun-Hua You, President of Shinewave