【2020 Application Example】 AOI fabric inspector lowers the false negative rate, and reduced the re-inspection volume by 70%

Low detection rate, slow speed, difficult recruitment and high personnel costs
The textile industry has always been a labor-intensive industry. At present, almost all textile companies worldwide still inspect fabrics manually. There are three major pain points in manual fabric inspection: Low detection rate, slow speed, difficulty in recruiting workers, and high personnel costs On average, a fabric inspector can find up to 200 defects in one hour with a defect detection rate of about 70%.
However, inspectors are only able to maintain their concentration for 20 to 30 minutes at most, and their fabric inspection speed is generally limited to 20 to 30cm/s. Fabric inspectors become fatigued if they exceed this time and speed.
Domestic and foreign AOI fabric inspection machines purchased by textile manufacturers have not yet been officially integrated into the production line. At the beginning, 10,000 suspected defects could be detected in one roll of fabric. The detection rate was high but the accuracy [screening] was low. The number of suspected defects has been reduced to 7000, but is still not at the level of experienced inspectors.

▲High-speed cameras capture defects and record their locations
The rule-based defect identification method currently used by manufacturers requires a lot of adjustment time (about 1 to 3 months) before the manufacturers (site) actually uses it, and there is currently no solution to automatically correct the identification model after use. As a result, manufacturers need to spend extra time to adjust parameters. Therefore, it requires considerable cost for both manufacturers and clients (sites).
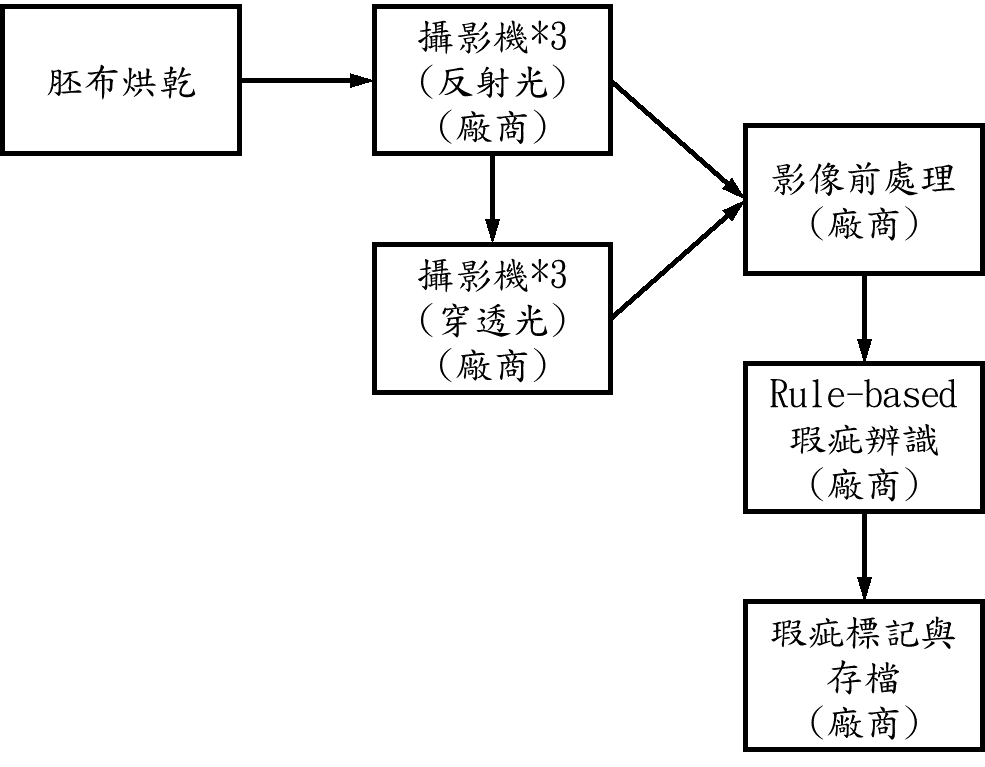
▲Current grew fabric inspection process of manufacturers
The specific method used by the guidance team and cooperating manufacturers to implement AI identification technology and learning framework (for model retraining) into the defect inspection process is described below
1. AI-based defect identification model:
Utilizes the large amount of image data collected (including fabrics with and without defects) to construct the defect detection model through machine learning, such as SVM, or deep learning object detection methods, such as SSD or YOLOv3. This model is used to determine the condition of the surface of grey fabric and determine if it is a normal product or a defective product, thereby achieving defect identification.
2. Identification model retraining framework:
If there is an error in the judgment of the visual inspector, the image will be marked and the data will be used in the dataset for re-training. After a certain number of misjudged data is accumulated, the system will automatically start the identification model retraining function, and the new model that is generated will automatically replace the old recognition model, thereby achieving the purpose of model update.
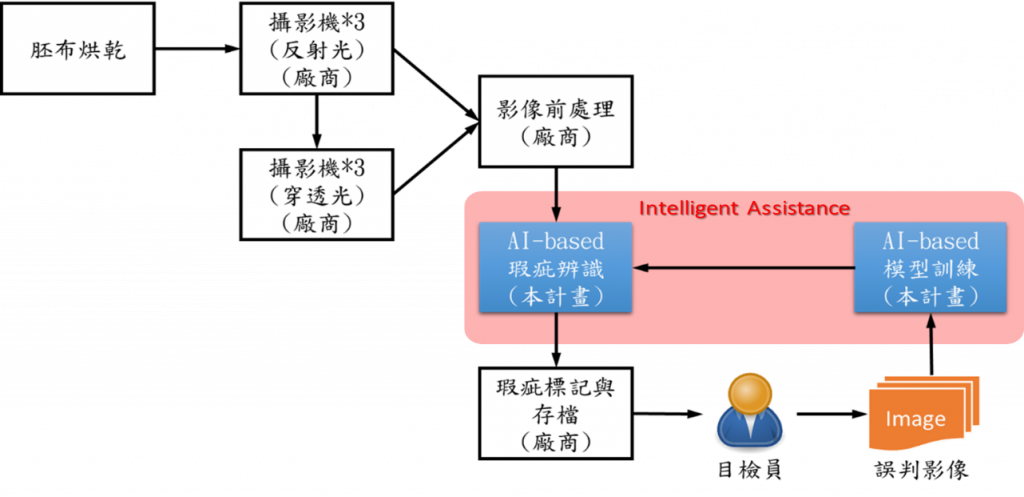
▲Grey fabric defect inspection process after the implementation of this project
Low false negative rate and solves the challenges of labor shortage and higher quality requirements in the industry
This project uses a deep learning network architecture to reclassify defects that are detected, including real defects and false defects, and can further classify real defects and false defects to lower the false negative rate of traditional AOI solutions. This is expected to reduce re-inspection volume by 70% and above for fabric inspectors, eliminate concerns about implementation in the current production line, accelerate the application of AI-based AOI solutions by textile manufacturers, and solve the challenges of labor shortage and higher quality requirements in the industry.