【2020 Solutions】 AI Enhancements, AOI Inspection Miss Rate at 0.1% Surpasses Manual Effort by 10 Times

Did you know a single golf ball can have up to 28 defect inspections? Manually, one can inspect 500 balls in an hour, but with AI, up to 6,000 balls can be inspected in the same time. Huiwen Technology has developed AOI (Automated Optical Inspection) technology that achieves a miss rate of 0.1%, which is ten times better than human inspection. Besides the golf ball industry, Huiwen Technology's AOI inspections are also being introduced to the textile industry and others.
Geng Cheng Lin, the founder and general manager of Huiwen Technology, has been an expert in artificial intelligence (AI) since 2013, recognizing the future potential and explosive power of deep learning (DL) and AI-based image recognition. AOI has always been a strong demand in the manufacturing industry, mainly to improve product quality for business owners, stabilize the quality of delivered goods, and use data from AOI inspections to improve processes, thus creating a virtuous cycle and further cost reductions.
Due to uncontrollable factors such as human eye fatigue and inconsistent standards, inspection encounters bottlenecks. The limit of human inspection miss rate after training is about 1-2%, and the situation worsens over time. AOI is a stable and capable of mass inspection device, achieving a miss rate of 0.1%, which is ten times that of human eyes, implying a detection rate of 99.9%. Of course, AOI also results in a 5%-10% over-inspection rate, which can be further screened manually. With the help of AOI, the burden of quality inspection is reduced, saving a considerable amount of labor time.
AOI Golf Ball Defect Inspection, Inspection Capacity Increased 12 Times per Hour
The first litmus test of Huiwen Technology's AOI technology was on golf balls. With their highly reflective, uneven surfaces, golf balls were previously inspected manually for defects. A tiny golf ball can have up to 28 defects, and traditionally, only 500 balls could be inspected per hour. A major domestic golf ball manufacturer, meeting the demands of Japanese customers, introduced AOI inspection two years ago. The high-speed, high-precision AOI system combined with AI deep learning image recognition technology conducts defect detection on golf ball surfaces, fully automates the feeding and outfeed process, replacing manual recognition of missed defects, and can immediately record defect conditions and report back, inspecting up to 200,000 packs of golf balls per year per machine, greatly enhancing customer satisfaction. However, this step took Huiwen Technology more than two years.

▲ Golf Ball AOI Recognition Image
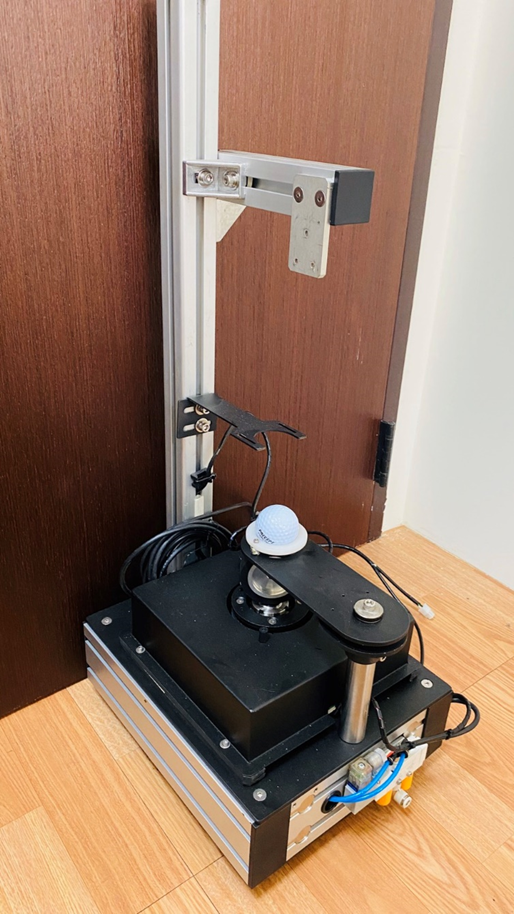
▲ Golf Ball AOI Recognition, 28 Surface Defects Unveiled
Lin Geng Cheng says, from data assessment and consulting, followed by data organization and tagging, selecting and verifying AI algorithms to AI training services, the golf ball data is like starting from zero, accumulating one by one. Thankfully, with full support from golf ball manufacturers, the efforts have finally bore fruit. With AI inspection, while manually one might inspect 500 balls in an hour, AI can handle 6,000, achieving effectiveness 12 times greater.
Unlike other companies, Lin believes that AI needs to delve deep into domains to scrape professional data since only with such domain data can AI perform well. Therefore, the company starts from individual projects, rather than setting an AI product from the beginning. Without quality data or a focused domain, the best algorithms cannot succeed in AI. Over the years, Huiwen Technology has accumulated project experience, gradually developing products while focusing on domain data and providing the latest AI algorithms to customers, growing together, creating a tighter collaboration, which is why, different from external fundraising, Huiwen's investors are customers or partners.
Evaluation to Official Launch: AI Introduction Requires Six Phases
The projects undertaken by Huiwen Technology are divided into several phases: 1. Evaluation period, 2. Initial Validation (POC) period, 3. Data Collection period, 4. Repeated Verification period, 5. AI Positive Cycle period, 6. Official Launch. The evaluation period involves understanding and assessing the Domain conditions of the demand side beforehand, followed by POC verification, extensive data collection after POC, entering repeated verification stage, and finally allowing AI to enter a positive cycle phase, achieving a certain level of effectiveness before the official launch. Generally, a project takes about six months to a year to develop. However, with more familiar PCB AOI projects, the first two stages are skipped, starting from data collection, thus significantly reducing the time.
'Regardless of this project or others, common questions from customers are: 'How much data is enough? When will AI learn?' Facing such questions, Lin points out that the reasons for these questions are: 1. The inexplicability of deep learning technology, as it is a black box; 2. Generally, customers lack the concept of AI technology. Thus, the company must patiently verify data repeatedly, identify the data needed by AI, accumulate and test it, and clarify and resolve all Domain conditions, which requires a lot of time and patience.
During the AI introduction process, customers have high expectations of integrating AI services, thinking that it can immediately replace human labor. Lin points out that this is not the case; the real value of AI lies in accumulating large volumes of high-quality data, which is then transformed and analyzed to establish AI training and verification models to fully address problems generated by manual processes.
Apart from inspecting golf balls, Huiwen Technology is currently targeting the textile industry for items such as fabric and shoelaces, and many industries have conducted POC trials through Huiwen, including the semiconductor industry, PCB industry, and other traditional industries.
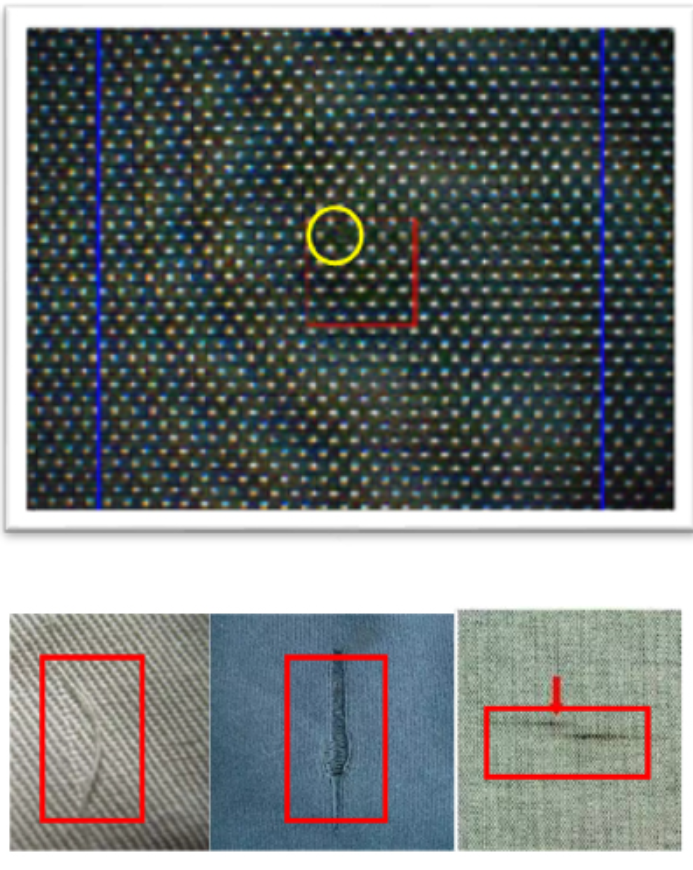
▲AOI Fabric Defect Detection, Top Image Shows Before AOI Inspection, Bottom Image Shows After AOI Inspection
Lin Geng Cheng indicates that the most difficult aspect of entrepreneurship is nurturing talent and customer recognition; customers often demand quick results, not realizing that AI adoption requires data accumulation and repeated verification, processes that cannot show results in less than six months.
Affected by the COVID-19 pandemic, the trend of globalization and centralization of the manufacturing supply chain has been disrupted, replaced by 'short region' supply chains, suggesting small, beautiful factories will flourish everywhere, potentially bringing new opportunities for AOI. Lin notes that high automation indeed offers opportunities for automatic inspection AI, however, relatively high capital investments, including automation equipment, mainframes, GPUs, and sufficient AI maintenance talents, are burdens that small and medium enterprises or small factories cannot bear, requiring government financial resources and input to facilitate smooth transformation.
「Translated content is generated by ChatGPT and is for reference only. Translation date:2024-05-19」