【2021 Application Example】 AI Complements the Disruption of Traditional Industry Experience: Production Forecast Analysis in Plastic Recycling Process
As the number of veteran craftsmen in traditional industries diminishes
In Taiwan, SMEs have always played a central role in Taiwan's industry, accompanying Taiwan through various 'economic miracles' periods. But as time progresses, the old masters gradually became elderly craftsmen. Coupled with the phenomenon of fewer children and changes in the overall industrial structure, fewer and fewer of the new generation are willing to enter traditional industries. Now, it can be observed that the main combination on most SMEs' operational fields is formed by 'elder craftsmen' together with 'foreign workers.' These experienced craftsmen, who act as living dictionaries of field experience, suffer from a lack of successors to continue the tradition, leading to a growing difficulty in sustaining on-site experience transfer in traditional industries.
The limits of traditional hands-on process optimization are in sight
Located in Tainan Baoan Industrial District, 'Tangxian Company' was established in 1972, initially manufacturing high-quality weaving equipment. It possesses the capability to manufacture machinery, and in recent years it has actively developed environmentally friendly plastic recycling equipment in response to international green energy, recycling, and environmental protection demands. Ultimately, they have successfully developed low energy consumption, low waste, high purity, and high output recycling granulators with a sleek and efficient machine design supplemented by advanced intelligent control technology.
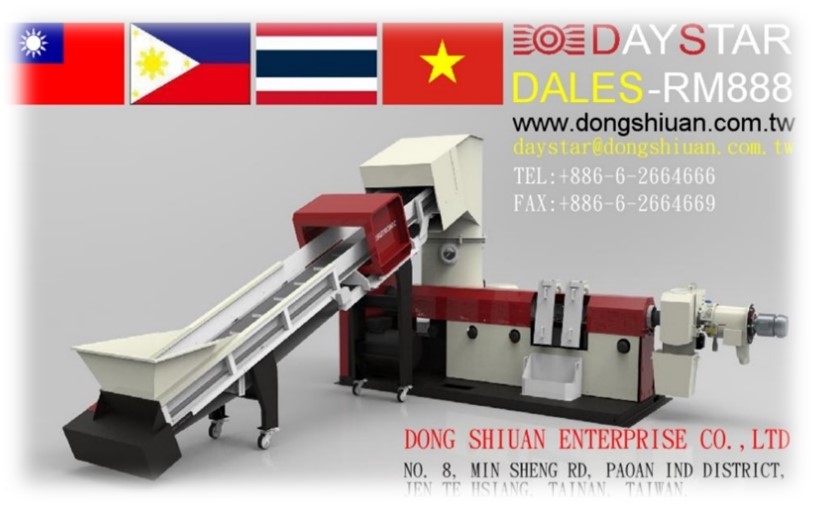
▲Tangxian Company's self-developed plastic recycling granulator equipment
However, in the production process of plastic recycling, when faced with hundreds of material types and dozens of process temperatures, speed settings, what is faced is thousands of possible parameter combinations. Previously, the adjustment of various production process conditions was reliant on the on-site staff (the experience of the craftsmen). Thus, during the transition of production of different incoming materials (such as PET, PP, PE), a significant amount of raw materials would be wasted during the trial phase.
The professional information gap in traditional industries
Tangxian Company recognizes the importance of data. In the past, although process parameters were recorded, due to a lack of data capabilities at the time, it was primarily in paper form, manually written down by the operating staff, accumulating a large amount of paper data. However, this also meant a lack of scientifically accurate and detailed information available for real-time reference and adjustment.
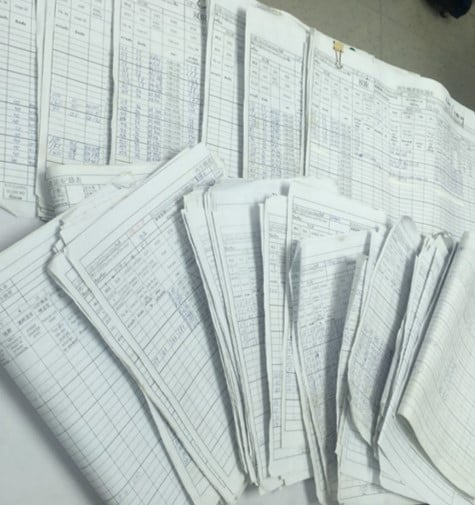
▲Process parameters logbook, records the state of about a dozen machines and production figures hourly
In quality control as well, due to a lack of control over the quality of output and monitoring and feedback mechanisms for unit time production, it becomes difficult to predict the profit conditions of each batch. Production management can only estimate and average cost and productivity changes over the process from the outcomes, without being able to objectively and timely restore the production conditions to reasonableness or make clearer adjustments when facing quality abnormalities.
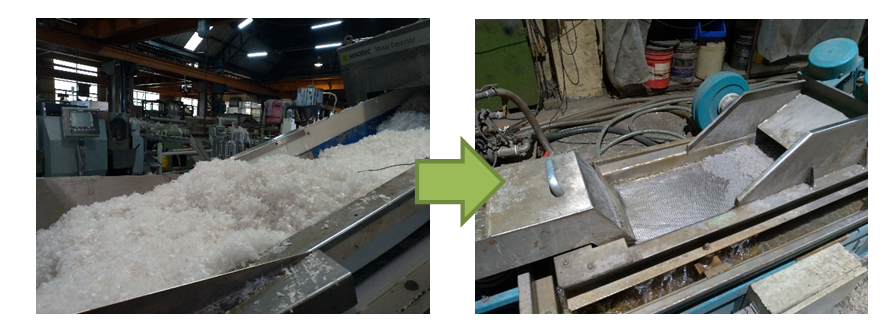
▲Site reality (left image shows recycled scraps; right image shows pellet production)
Taiwanese manufacturers possess strong machinery manufacturing capabilities, and many modern machines now have data capabilities, recording real-time status and information via IoT. But is the infrastructure of the factory's on-site and information systems ready yet?
When the Old Master Meets AI
With government referral, Tangxian Company partnered with a Taiwanese data science company, working together to integrate AI services and optimize internal processes using AI. They started with a medium-sized plastic recycling production line within the factory as a trial field. After establishing a successful benchmark, this model was expanded to larger plastic recycling machinery within the factory to continue verification and application.
Initially, both parties converted the past handwritten paper data into digital format using OCR supplemented by manual correction. Tangxian Company also worked with the supplier of the human-machine interface of the machinery to integrate the control panel and parameter data into the factory's database, allowing real-time monitoring of machine status and eliminating the complexities and potential errors of manual transcription.
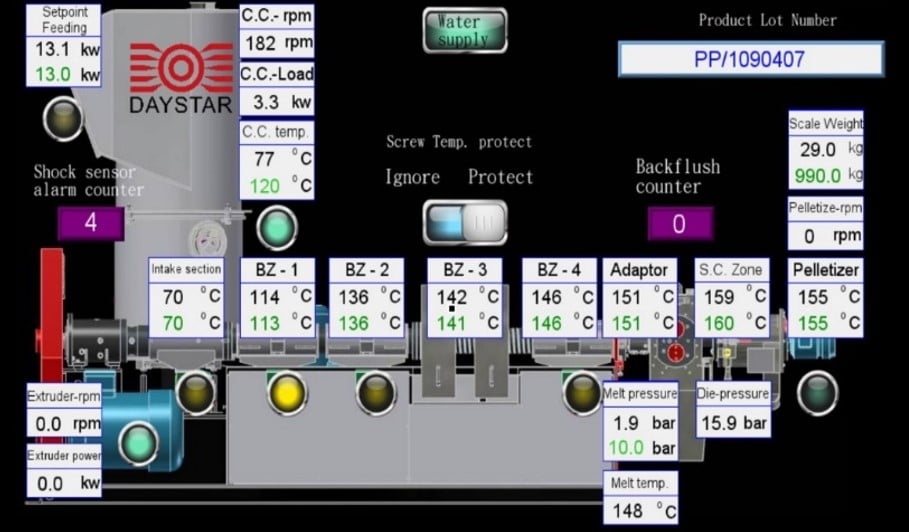
▲Panel of plastic recycling granulation machine, showing current process temperatures, speeds, and power usage
Meanwhile, the Taiwanese data science company further modeled dozens of parameter data through AI, conducting scenario analysis to simulate various production possibilities under environmental parameters and material inputs, identifying key characteristic parameters and providing parameter adjustment recommendations to decrease costs during the trial phase.
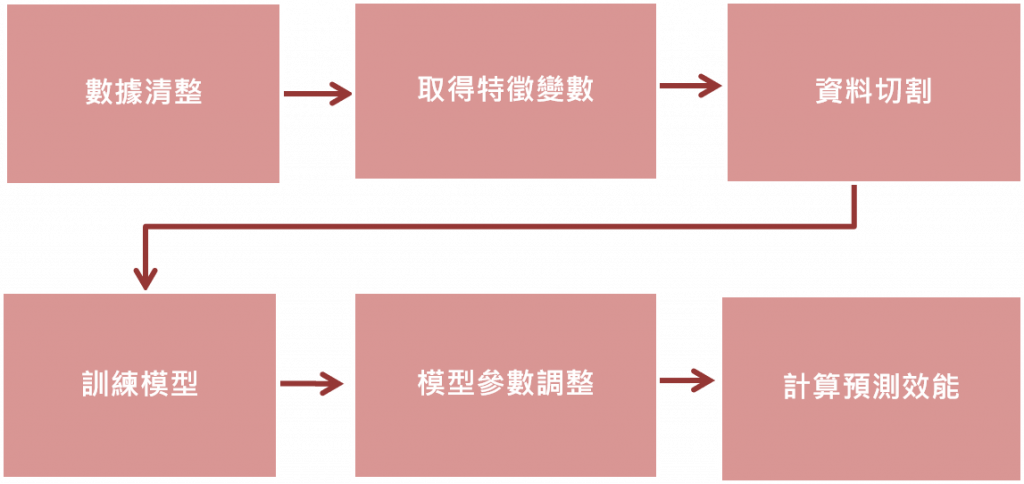
▲Applying data analysis to traditional industry machinery processes
After the old master receives the raw materials, they only need to enter the relevant material characteristic parameters, and the system automatically generates recommended process parameters. After small adjustments by the old master, they proceed with the trial production of the material, effectively reducing the waste of materials, water, electricity, and manpower caused by incorrect attempts. Moreover, Tangxian Company has proactively deployed the concept of 'production pedigree' in the plastic recycling process, allowing the batch's raw materials and process parameters to be accessed by scanning a QRCode.
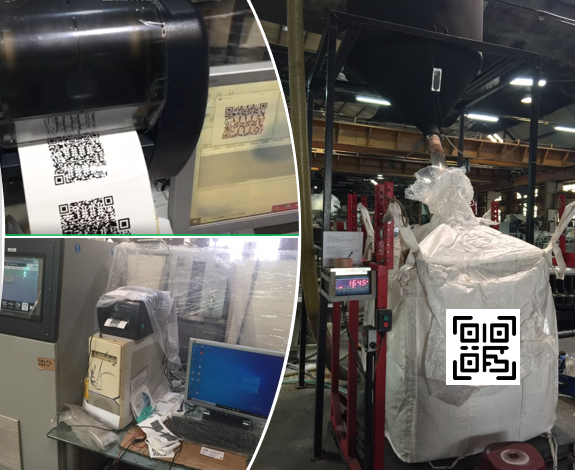
▲Production and sales pedigree of plastic recycling pelletizing
Taiwan's SMEs have strong machinery capabilities, just waiting for the 'east wind' of data
From industrial revolutions 2.0 to 3.0, even 4.0, many Taiwanese SMEs face challenges in transitions not just in upgrading machinery, but after investing in modern equipment and generating data, they do not know how to utilize it effectively. It is impractical for these manufacturers to develop a specialized data analysis department on their own; meanwhile, Taiwan also has many innovative teams with strong software capabilities in AI and data analysis, possessing the technology but lacking the field and data. Therefore, if the traditional industries of Taiwan could be fully integrated with the innovative teams in AI and data analysis, it would not only address the current challenges of manpower and experience transfer faced by traditional industries but also advance Taiwan's development and application of AI significantly.
「Translated content is generated by ChatGPT and is for reference only. Translation date:2024-05-19」