【2022 Application Example】 Droxo Tech Applies Drones in Golf Courses to Reduce Manpower by Half

For most golf courses, the operations and management is a headache. "Golf courses are selling turf and need to be properly taken care of," a golf course manager bluntly pointed out. Facing the market pain points of labor shortage, aging population and high cost, the use of AI drones for pesticide spraying and pest control will reduce labor costs by more than half and greatly improve the overall operational efficiency.
At noon in early summer, an AI drone is slowly taking off at the Taipei Golf Club in Taoyuan. Its main task is to test AI drone fertilizing and pesticide spraying on the golf course. In fact, drones of Droxo Tech, the company performing this task, are widely used for fertilization, pesticide spraying, and pest and disease control for rice, bananas, and tea trees. For golf courses with turfs that often cover tens to hundreds of hectares, AI drones are needed to assist in turf maintenance. Data collection, development of pesticide spraying AI models, and multispectral image analysis and testing will be carried out in the current stage. In the future, large-scale technology implementation and verification will be carried out to set an example for applying drones to golf courses.
Using AI drones to fertilize and spray pesticides can reduce the manpower required by half
The traditional way of maintaining the turf in golf courses is to carry spray buckets or drive spraying vehicles to spray areas one by one. "Domestic golf courses began to plant ultra-dwarf Bermuda grass in 2001. This grass species prefers a cool climate and is not suitable for Taiwan's hot and humid weather." Droxo Tech’s CEO further pointed out that to prevent turf from pests and diseases, pesticide spraying is necessary. For an 18-hole golf course, it is equivalent to spraying pesticides once a week, and the T-ground and fairways are sprayed every two months. For golf courses, spraying pesticides is time-consuming and labor-intensive. It is important to note that large-scale spraying will increase the risk of personnel poisoning and increase the amount of pesticide used.
▲Benefits of applying agricultural drones to golf courses
According to Droxo Tech’s research, golf course pests include Spodoptera litura, which comes out at night to look for food, so pesticide spraying must be carried out in the evening. According to the traditional method, pesticide spraying requires two vehicles and three personnel for a total of 4.5 hours. If AI drones are used for fertilizing and pesticide spraying, it only takes one operator to spray 0.8 hectares of land in 20 minutes, saving about two-thirds of the manpower and reducing operating costs by about 30%.
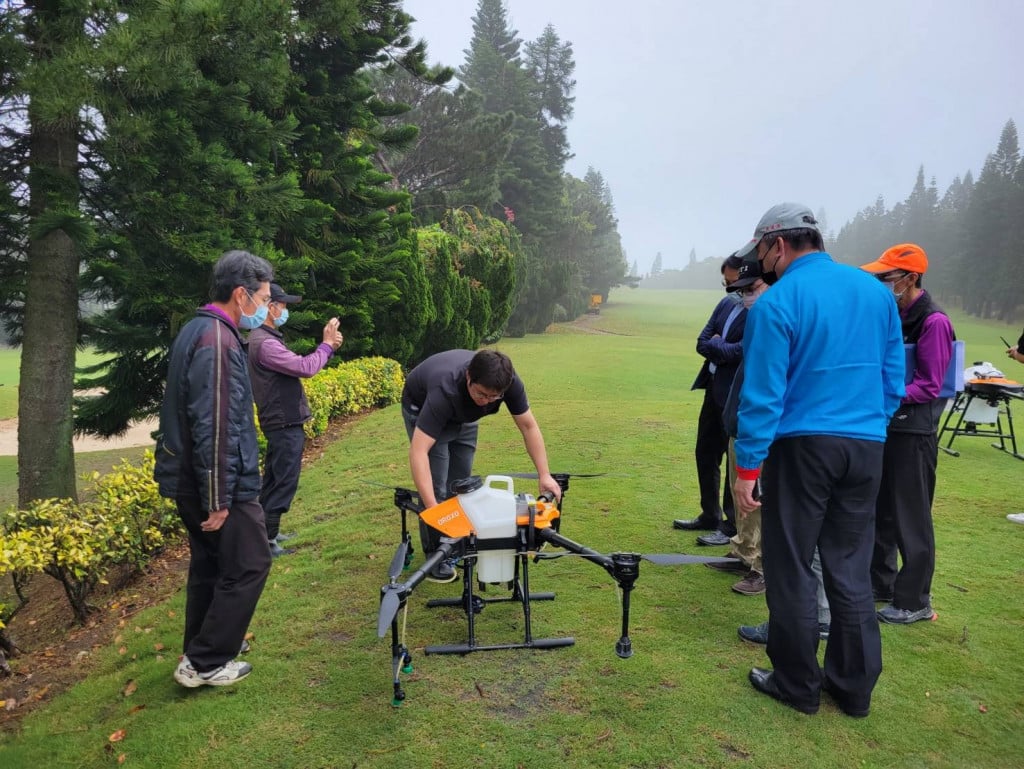
▲Using AI drones to fertilize and spray pesticides on golf courses can reduce the manpower required by half
In addition to the significant benefits of using agricultural drones for golf course turf maintenance, Droxo Tech also specially introduced AI multispectral image recognition for NDVI (Normalized Difference Vegetation Index) analysis. "The so-called multispectral is to direct light with different wavelengths on the turf, and the reflected images are collected for analysis." Droxo Tech CEO Liu continued to explain that each plant absorbs light with different wavelengths, so multispectral imaging can determine the growth status of grass species. At the same time, combined with AI image recognition, the distribution of pests and diseases can be accurately detected, and the amount of pesticide used is determined on this basis.
Cross-domain collaboration to build a multi-source turf image database
Using AI multispectral image recognition technology, Droxo Tech will collect visible light, multispectral, thermal images, and hyperspectral images to establish a multi-source turf image database to fully understand the growth cycle of Bermuda grass. Droxo Tech has accumulated rich experience in agricultural AI drone pesticide spraying , but there are still many problems that need to be overcome to implement AI solutions in golf courses. For example, it is necessary to establish a new pesticide spraying model and test flight methods, especially the application of multispectral image recognition. PoC is not difficult, but actual implementation requires more test evidence, repeated inferences, and collaboration with plant experts. This part must rely on the cross-domain integration of legal entities such as the Institute for Information Technology (III), gathering more fields for verification, and creating a paradigm before it can be more widely adopted by golf courses.
There are not many international cases on the application of AI drones in golf courses. During the verification process, it is not yet known whether it can be quickly copied to the next golf course. However, Droxo Tech CEO Liu believes that through cross-domain collaboration, clearly defining the problems and listing them one by one, supply and demand parties can reach a consensus, propose solutions to each problem, and seek cooperation with internal and external resources. Only then will we be able to gradually achieve the goal of making golf courses smarter and smoothly assist the industry with transformation.
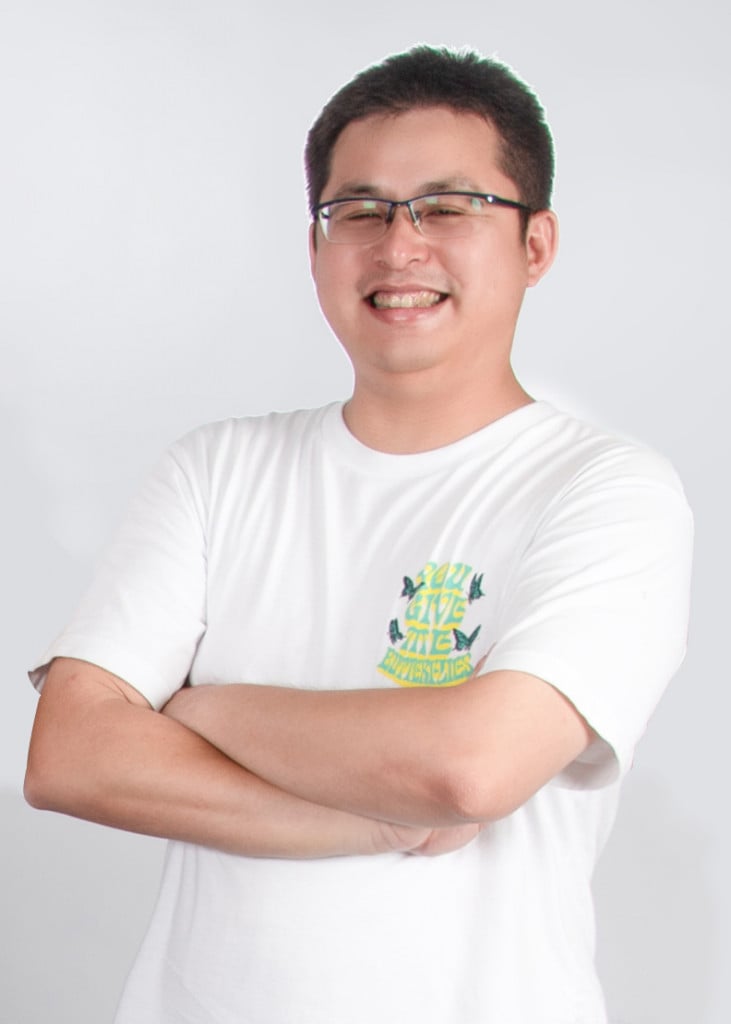
▲Zuoyi Technology's CEO, Liu Junlin
「Translated content is generated by ChatGPT and is for reference only. Translation date:2024-05-19」