【2021 Application Example】 HRT Technology Improves Production Efficiency by 20% Through AOI Detection of Defects in VCSEL Packaging

In 2017, the launch of the iPhone X made 3D sensor technology used in Face ID highly popular, which drove the development of VCSEL, a core component in the 3D sensor module. In the detection of defects in incoming packaged VCSEL, the use of AI inference models can solve the industry's issue with low yield and improve reliability to 95%.
VCSEL technology currently can be used in many applications and various end consumer markets, including robots, mobile devices, surveillance, drones, and AR/VR. VCSELs are a good solution in applications that require high-speed modulation capabilities, such as cameras and biometrics.
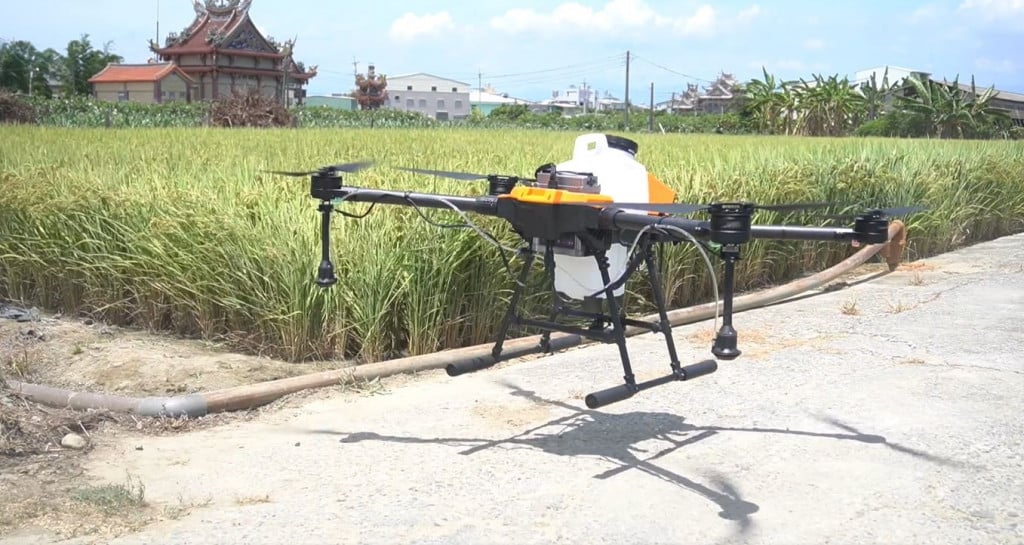
▲VCSEL technology has a wide range of applications, including in drones. (Pictured: Zoyi Technology's Agricultural Drone)
VCSEL technology has a wide range of applications, AI technology assists in defect detection
HRT Technology stated that the packaged VCSEL market is also facing strong price competition from competitors, and needs to further reduce costs and enhance product competitiveness. One of the key problems is the replacement of glass lens with epoxy resin lens. The production of traditional glass lenses has high yield, but the cost is higher than that of epoxy resin lenses. Due to the cutting process of epoxy resin, the side wall of cutting lines can easily have rough edges, causing it to be oversized. The release of stress caused by heat during the mounting process will directly cause the optical lens to break.
HRT Technology pointed out that the incoming inspection of VCSEL epoxy resin lenses is very important. Under the constraints of packaging space, the space for fitting the package and optical lens is limited. Moreover, the optical lenses will be confined to a metal frame. If the dimensional tolerances are properly controlled, stress release due to heat during mounting can easily cause the optical lens to break, resulting in a yield loss of up to 10% in the VCSEL package reliability verification, resulting in an increase in production costs.
In order to solve the problems above, HRT Technology hopes to use AI to monitor the size and appearance defects of epoxy resin components in the VCSEL epoxy resin lens incoming stage, verifying whether their dimensions meet specifications, whether the cutting edges are smooth, and whether there are any defects in their appearance. Since traditional incoming material inspection requires a rough visual inspection by humans to distinguish the quality. The problem of image collection needs to be solved first to successfully collect image data.
Therefore, HRT Technology first developed an Automated Optical Inspection (AOI) device, which includes X, Y, Z three-axis motion, high-resolution cameras, and related control software to automatically record images. After collecting the image data, opencv aligns the test image and a normal image to determine differences between the two images, and then pixel mapping is used to compare the pixel area to complete initial screening. Manual labeling is carried out according to the image classification above, including: samples that are normal, have defects in appearance, or have different shape characteristics, and then algorithm training and verification is carried out. Residual neural network (ResNet) or other related algorithms are used for deep learning to identify the quality of lenses.
Implementation of AOI inspection improves production efficiency by 20% and above
Comparing the differences before and after the implementation of AI image inspection, the incoming VCSEL lens inspection before implementation only involved manual inspection of the appearance. The lens is packaged on the VCSEL package that has completed die bonding. After passing the general light up test, the final reliability test (high temperature reflow) is performed. Failed samples go into the rework process.
However, after the implementation of AOI inspection, it can screen defective lenses sooner and reduce the cost of subsequent materials input, it can also reduce the need for rework due to failure, improving yield to 95% and above in the reliability verification. This is expected to help companies reduce production costs by 10% and increase production efficiency by 20% and above.
▲ The difference before and after implementing AI image detection
HRT Technology pointed out that this technology is an AI application developed based on tiny images. It uses deep learning algorithms to identify defects in the images. The trained network automatically classifies image data to predetermined categories. Defect categories can be determined through reference images, so cumbersome programming is not required.
In the industrial machine vision environment, deep learning is mainly used for classification tasks in applications, such as inspection of industrial products or identification of parts. In the future, with the development of IoT wearable devices and the trend of energy saving, the size of optoelectronic components will continue to shrink. This technology can be applied to the detection of defects in the appearance of other tiny optoelectronic components in the future.