【2020 Application Example】 AI constructs the best coating model to reduce the inspection cost of scrap electrical steel sheets, saving NT$2 million per year

Surface treatment applications face rising costs and talent gaps
The development of metal surface treatment technology affects the quality of aerospace, automobile, machinery, home appliance, communications, and fastener products sold domestically and exported. At the same time, it plays a pivotal role in domestic smart machinery, national defense, and circular economy in the " 5+2 Industrial Innovation Plan." According to 2018 survey statistics, the output value of the metal surface treatment industry reached NT$151.5 billion, an increase of 3.6% compared to 2017.
However, metal surface treatment is a labor-intensive, energy-consuming, and pollution-intensive industry. It has long suffered from a shortage of professional and technical talent, and the tightening of environmental regulations has caused processing costs to continue to rise. As a result, the industry is facing a crisis of survival and a crisis of competition from international high-value supply chains.
Manual quality control faces market challenges, while the coating process has found new opportunities
Overseas markets currently account for 70% of the revenue of a domestic steel plate coating plant. It expanded into the automotive steel, diverse supply chain, and various special steel product markets in 2016. It is imperative to improve the quality of surface treatment through innovative technologies, in order to seize international markets.
In the continuous steel plate coating process, the price difference between finished steel plate products and defective products is about 10 times. Manual inspection is used in the current stage. During the production process, 10 m needs to be cut from each steel coil and becomes fixed inspection waste, incurring a significant amount of cost for waste materials, and also delaying production. At the same time, the instability in manual inspection quality also makes production quality unstable.
The Southern Taiwan Industry Promotion Center (STIPC) utilized the guidance capabilities it accumulated over a decade in Southern Taiwan, and matched the steel plate coating plant’s pain point with an AI optical measurement technology service provider. This reduced the cost of consumables used in steel plate inspection, and reduce errors caused by fatigue during manual inspection.
Stabilizing steel plate coating quality with optical measurement technology
In order to control the quality of the coating process, image recognition must be used to identify product yield. General measurement technology requires contact to detect the thickness of coating. Therefore, the STIPC match the plant with an AI optical measurement technology service provider to assist in the development of a non-contact optical measuring instrument, record coating data, and then compare the data to obtain the best process parameters.
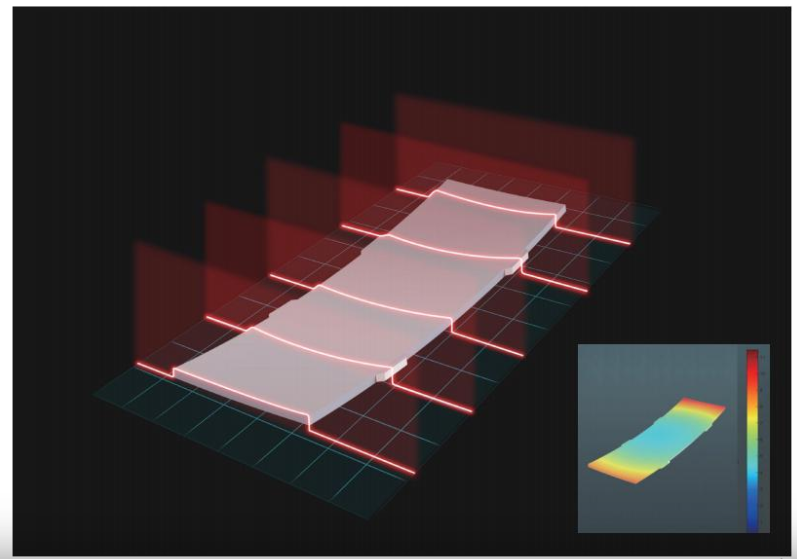
▲Illustration of 3D non-contact measuring instrument testing
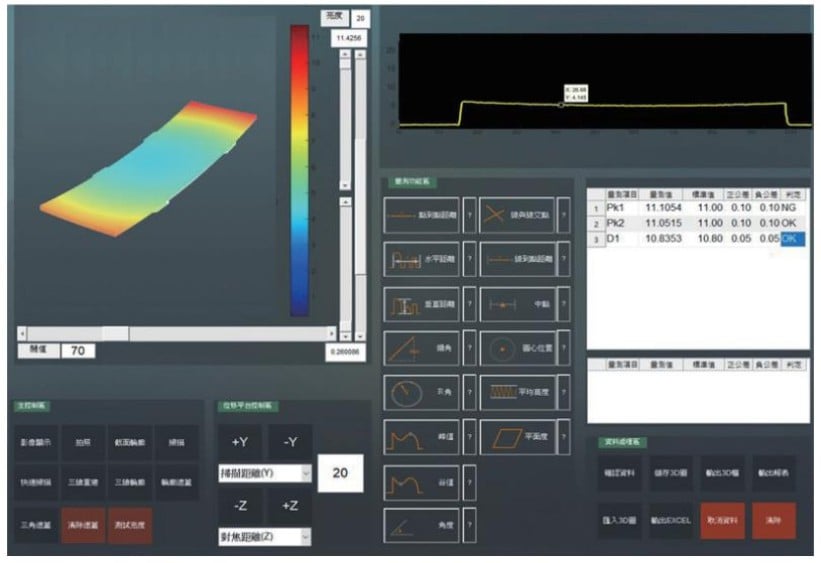
▲Presentation of measuring instrument data
Rapid scanning through AOI achieves non-contact measurement. It can quickly scan the profile and overall dimensions of the object being measured without directly making contact with the product or damaging the surface of the steel plate. It can immediately control coating thickness and quality of steel plates without increasing cost. We hope to calculate data of the process environment and design the product abnormality warning range, so that it can be used to make the process smarter.
In the future, this solution will further detect surface defects and color differences of finished steel plates to reduce the proportion of discarded material, solve the problem of the gap in professional and technical talent, and improve product yields.
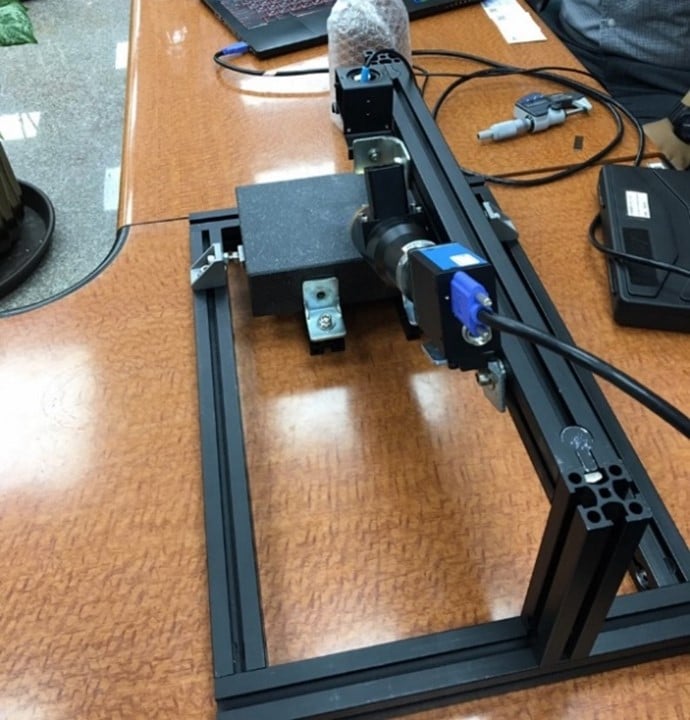
▲Schematic diagram of non-contact measuring instrument
Establish an AI coating model to create world-class steel plate supply standards
With the guidance of the STIPC in 2020, the steel plate coating plant accelerated the application of advanced process technology and established quantified indicators of surface treatment process quality standards, which will help domestic surface treatment companies produce high-quality electrical steel sheets, and is expected to increase the product price by 2%.
In addition, it can also assist companies in the industry obtain heat treatment certifications for high-value aerospace, electric vehicle, fastener, and aerospace products, increasing the industry’s added value through innovative thinking, and continuing to lead the metal industry forward.