【2020 Application Example】 AI Smart Customer Service Maintenance Response System, solving customer machinery fault issues instantly through chatting!
A tool machine manufacturer that markets successfully both domestically and internationally, but also faces challenges?
A domestic tool machine manufacturer specializing in CNC wire cut machines, CNC EDM machines, and CNC fine hole EDM machines, uses its strong core capability in electromechanical development to deliver high-precision, high-quality products. It has successfully developed an aviation engine turbine ring wire cutting machine and specializes in designing and manufacturing super-large custom models, successfully marketing its products to over 30 countries worldwide.
Though capable of marketing high-quality products, the lack of standardized processes and methodologies for machine maintenance means that it often requires significant manpower and time to address machine failures, increasing maintenance costs...
No fast repair solutions, difficult personnel training, high maintenance time costs
While the tool machine manufacturer can sell high-precision machinery globally, encountering maintenance situations always consumes a lot of manpower and money. This is due to the lack of standardized troubleshooting processes for machine maintenance, mainly relying on the experience of maintenance technicians and the machine error codes. Not all faults can be diagnosed through codes. Technicians can only initially judge based on the error codes, then hypothesize the likely fault causes for further inspection and maintenance. There is also no standard way to record the repair methods, making it difficult to quickly troubleshoot similar issues in the future.
In addition to 'lack of standardized fault troubleshooting process', there are also issues of 'difficult personnel training' and 'high maintenance time costs'. Technicians need years of repair experience and must be familiar with mechanics, electronics, and mechanical engineering. If error codes are not available during repair, it requires considerable time to identify the problem with the machine, causing significant time and cost losses.
▲Traditional way of addressing issues through email
Implementing the 'AI Smart Customer Service Maintenance Response System' reduces costs for maintenance visits, shortens the duration of repairs, and simultaneously enhances the product's value.
Considering the pain points mentioned, the needs of the tool machine manufacturer are threefold: firstly, establishing a 'fault troubleshooting AI image recognition maintenance knowledge base system'. Then, collecting data on machine failures to establish a 'machine fault condition database'. Lastly, integrating AI image recognition and deep learning functions to analyze photos taken at the time of the machine's failure in order to identify the most closely related fault issues and troubleshooting methods.
This 'AI Smart Customer Service Maintenance Response System' predominantly uses 'supervised learning' as its primary AI technique. The 'AI model' part involves 'CNN' (Convolutional Neural Networks), which is used for image recognition and obtaining extensive training data on machine malfunctions and recommended maintenance methods for effective AI predictions. The 'data analysis' part uses 'DNN' (Deep Neural Networks) to acquire reference data related to fault conditions after training, providing answers that maintenance staff and clients desire for repairs, reducing the rate of maintenance visits and enhancing the product's added value. Additionally, 'AlexNet' is used as a preliminary development tool; its parameters can be set independently and executed automatically, ensuring that the AI model trained aligns closely with expected outcomes.
Currently, the tool machine manufacturer has around 10,000 graphic and text entries, predominantly 'image data'. The system uses images for fault identification and text to assist in the diagnosis of abnormalities. It employs '360-degree panoramic modeling' to archive graphic data and stores numerous image files internally. Additionally, it gathers relevant data such as electrical currents, voltages, water pressures, and flow rates via sensors, utilizing them for associated decision-making processes. The following pictorial representation shows the system service process:
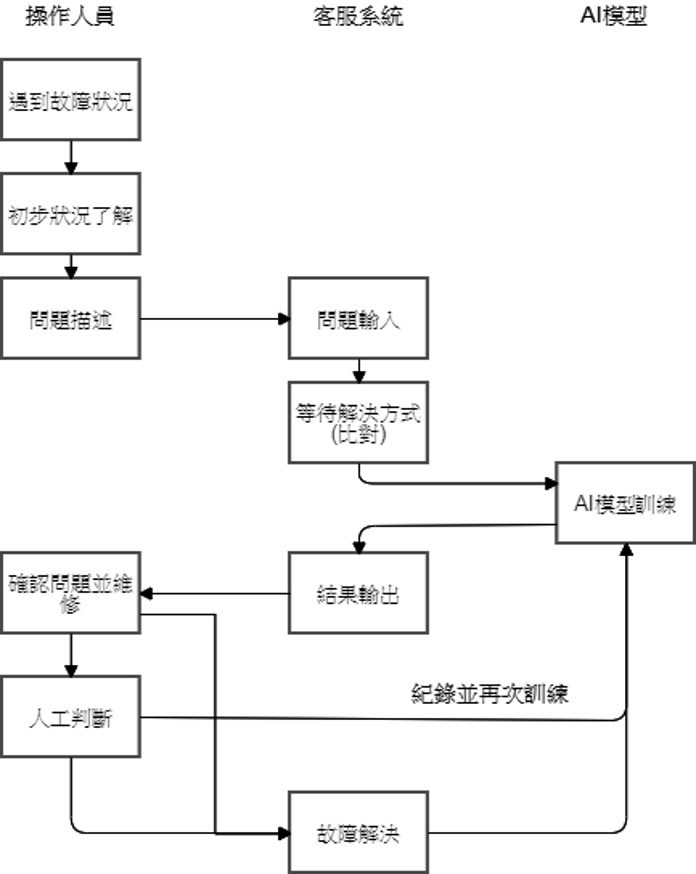
▲AI Smart Response Customer Service System Service Process Chart
This system gathers experiences from technical maintenance staff and information on machine faults to establish databases containing: machine fault conditions, machine fault images, maintenance actions, and completions of machines. It logs the comprehensive repair records, and leveraging AI image recognition and data analysis, it determines the most likely fault conditions. Through accumulated maintenance experience, the machine is enabled to autonomously learn and decide, offering the most suitable solutions to technicians or clients, thus shortening the training and repair time for technicians, reducing clients' downtime and costs, and increasing the machine's additional product value.
Promoting the 'AI Smart Customer Service Maintenance Response System' across various industries for greater economic impact!
This 'AI Smart Customer Service Maintenance Response System' initially sets up a maintenance knowledge base, then employs Chatbot technology to integrate smart customer service, allowing clients to interact directly via chat to quickly resolve basic machine faults. In the training of maintenance technicians, AI can also swiftly classify and inform of the likely fault causes and troubleshooting steps, thus lessening training and repair duration. By effectively solving issues like the lack of quick repair solutions, difficulty in training personnel, and high maintenance time costs, it is poised to expand its applications to other industries for more significant economic outcomes in the future.
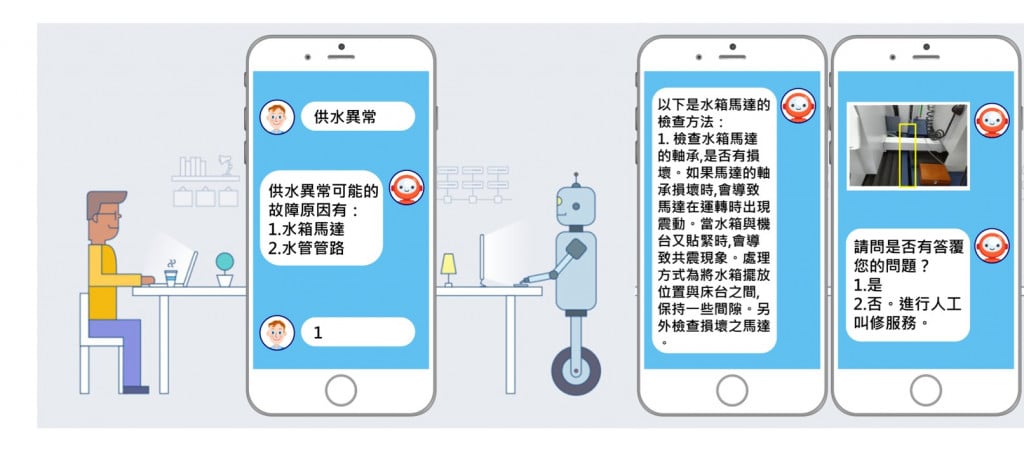
▲AI Intelligent Reply Customer Service System - Smart Image Recognition Customer Service Illustration
「Translated content is generated by ChatGPT and is for reference only. Translation date:2024-05-19」