【2020 Application Example】 "AI Color Recognition and Cost Optimization Control System" automatically recognizes colors, breaks through the traditional color grading model, significantly reduces costs, and improves yield!

Mixing new colors relies on the experience of master craftsmen!
The so-called "computer color matching" in the paint industry is simply the selection of "existing colors" for mixing, but there is actually no way to mix paint for a “new color” and it all relies on the experience of master craftsmen. Hence, it is necessary to start from scratch when a new color is encountered, which consumes a lot of manpower and time. Moreover, due to the different color mixing habits of each master craftsman, the cost can be significantly different despite producing the same result!
The trilogy when paint factories face the crises of transformation
I. Lack of color mixing standards
Generally, when traditional paint factories produce new colors, they will use a "spectrophotometer" to measure the LAB value of the sample color, and then the paint mixer will mix the paint of that color based on past experience. After color mixing is completed, the instrument will be used to test the LAB value and C and H wavelength. This process does not have a complete system and database records, and there are not standards for color mixing.
II. Production costs are difficult to control
Paint factories produce many pigments with different materials and functions, and the cost of paint will vary depending on the "color masterbatch material" used. Even if the color number of the masterpiece is the same, the cost will be different if the ratio of the color masterbatch is different. Paint mixers do not have a set of color mixing standards when mixing paint, making it difficult to control production costs.
III. The color grading process is lengthy and personnel training is difficult
As instruments cannot replace manual color mixing, the training of a paint mixer requires years of experience in paint mixing, familiarity with chromatology, as well as basic understanding of hue, saturation, and brightness. If there is no basic reference color values when mixing paint, the paint mixer must spend a lot of time repeatedly mixing colors, resulting in a loss from time cost.
Developing an "AI Color Recognition and Cost Optimization Control System"
The paint factory engaged in industry-academia collaboration with the Department of Computer Science & Information Engineering of Chaoyang University of Technology through CDIT Information Co. Ltd., and utilized the university's AI research capabilities to jointly develop the "AI Color Identification and Cost Optimization Control System." It established a database of "paint color numbers" and "color masterbatch material cost," and analyzes the optimal color mixing and optimal cost formula through data mining methods. The paint mixer can refer to the formula analyzed by the system for color mixing, and then input the formula into the system after paint mixing is completed. The formula is fed back to the basic database and an "artificial neural network model" is used by the system for deep learning, establishing a color grading standardization system for cost control and data collection, so as to solve the current difficulties faced by paint factories.
In the early stages of system development, CDIT planned the system requirements of the paint factory, established the system architecture and system database, and then worked with Chaoyang University of Technology on the implementation of model functions for the application of data mining and artificial neural network.
After the system is completed, CDIT will assist the paint factory in system testing and correction. The system will be introduced after correction and testing are completed, and training on system use will be provided to ensure the correct use of the system.
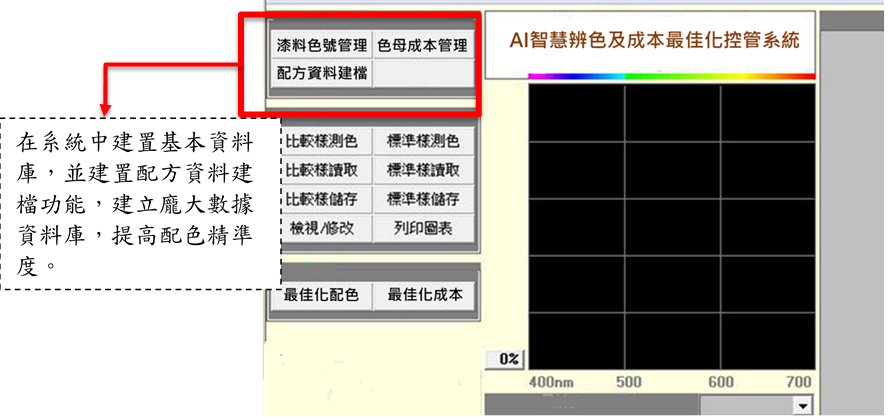
▲System Screen
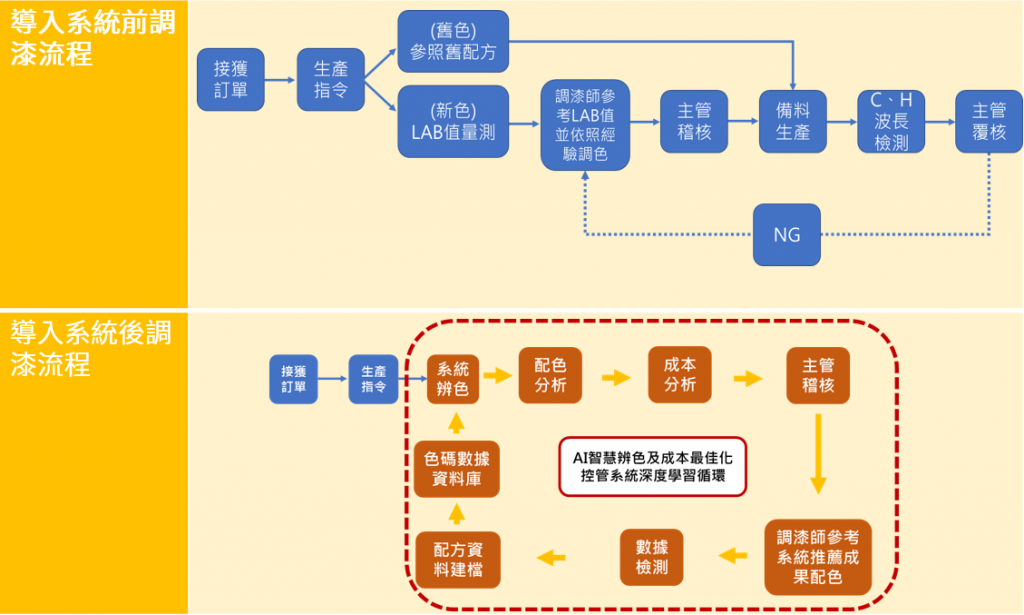
▲Differences before and after using the system
Expand new markets for the paint industry to see the paint industry thrive!
The "AI Color Recognition and Cost Optimization Control System" collects the color mixing formulas of paint mixers, establishes a paint color masterbatch formula database, and records the cost of each color number. The system's deep learning function is then used with a spectrophotometer to analyze the optimal color mixing formula for each data entry, so that the paint factory can control the cost of paint mixing. The optimal color mixing formula recommended by the system increases the speed of paint mixing and increases output value.
Future benefits include: The improvement in product yield reduces customer complaints and improves customer satisfaction. The breakthrough in the traditional color mixing model improves corporate image. Improves the efficiency of paint mixing, and allows the remaining time to be invested in training to enhance the professional capabilities of personnel. It will also allow the joint expansion of new markets with the paint industry and learning of new application technologies, and promote them to other paint companies, enhancing the industry's overall competitiveness to see the paint industry thrive!