【2020 Application Example】 Dynamic License Plate Recognition System: Time-Saving and Convenient for Management
Jiude Songyi Company, with 40 years in motor-related equipment manufacturing, introduced a dynamic license plate recognition system with an accuracy rate of 98.9% to effectively monitor vehicles entering and exiting the factory area. The system uses AI technology, making vehicle management both time-efficient and effortless.
License plate recognition systems are a fundamental application of intelligent image analysis. Using cameras to capture images of license plates, the system then analyzes and processes these images to recognize the plates. Kangqiao Technology, established in 2008 by a team of LED developers and software engineers, specializes in LED product applications, developed license plate recognition and Etag integrated systems, primarily for domestic and international public works projects.
Recently, the III AI Team collaborated with the Taiwan Energy Technology Service Industry Development Association to explore real-world applications of license plate recognition technology. They identified three major issues faced by Jiude Songyi Company at this stage:
1) Currently, the company gate has no barrier machine or other control equipment. Vehicle entry and exit rely entirely on manual control and recording. If no personnel are present, vehicle movements cannot be controlled
2) When issues arise, the existing surveillance system has to slowly search for data to locate the problematic vehicle, which is very time-consuming and inconvenient
3) When the footage is found, it is often difficult to clearly identify the license plate, and even if found, it is not possible to verify the vehicle owner
Solving Three Major Problems, Providing Four Major Functions
After understanding the actual needs of the enterprise, according to the license plate recognition system architecture established by Kangqiao Technology, real-world validation was conducted on-site, with monitoring computers set up in the control room.
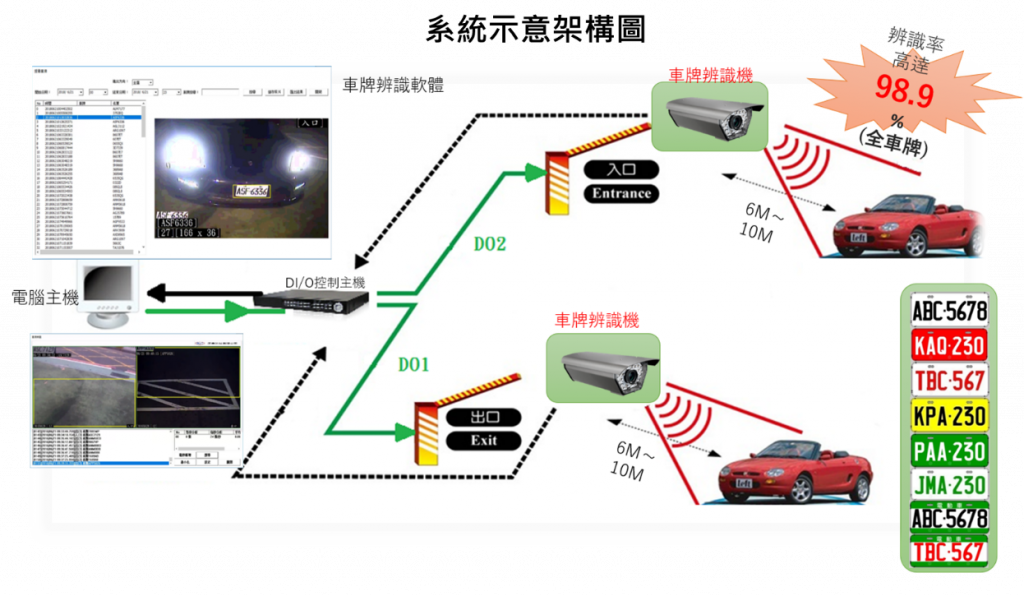
▲ Kangqiao Technology License Plate Recognition System Architecture
After installation, the main functionalities of the license plate recognition system are as follows:
1) When vehicles enter or exit, high-resolution smart cameras can identify license plates and capture images, recording the license number and vehicle status
2) When file retrieval is needed, vehicle data can be searched by time or license plate information, allowing quick access to the required video files, saving considerable time
3) The use of high-resolution smart cameras significantly improves image quality, which helps in clear identification in case of incidents
4) With registered license plate data, a blacklist and whitelist database can be set up, facilitating the management by security personnel
The advantage of license plate recognition is that it fully automates vehicle entry and exit control, reducing labor costs. The software helps to prevent misuse of license plates and eliminates the issues of remote control, induction buckle loss, and borrowing by unauthorized persons. Vehicles can enter and exit without using a remote control or rolling down the window. The long-distance license plate recognition allows gates to open while the vehicle is still moving, eliminating the waiting time for parking.
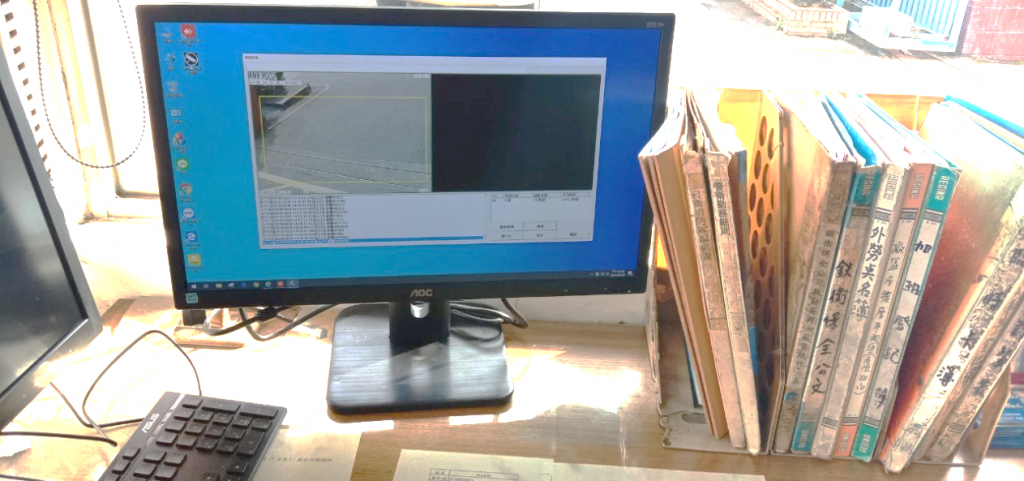
▲ Kangqiao Technology License Plate Recognition System Setup in the Management Room
The III AI Team states continually collaborating with relevant associations, from identifying corporate needs, setting topics, linking teams, introducing real-world validations, to systematically assisting enterprises in need to adopt AI technology and solve industrial problems, aiming for the AI transformation of industries. In the future, it will continue to help enterprises harness technology tools to overcome business challenges.
「Translated content is generated by ChatGPT and is for reference only. Translation date:2024-05-19」