【2020 Application Example】 Peeking into a Baozi to See How AI Reduces Scrap Rates by 50% and Boosts Production Efficiency by 60% for Frozen Foods

From production line to dining table, who oversees the hygiene management of what we eat?
In recent years, there has been a continuous stream of news reports concerning food safety, such as repackaging expired goods, and poisoning incidents at Hong Rui Zhen. It's clear that people are increasingly concerned about the hygiene of their food. However, due to various quality control methods in food processing, there are inherent risks.
The World Health Organization (WHO) has pointed out that unsafe food and water cause physical harm to 2 million people each year. Hence, international markets demand that food processing companies must establish a traceability system for products. This is why major domestic food processors also aim to set up a production traceability system to quickly trace back to problematic raw materials and initiate recall and destruction of problematic food.
Visible assurance, implementing production transparency
A major domestic food manufacturer producing frozen food and instant meals has expanded its market presence to North America, New Zealand, Japan, etc. They are also at the forefront in promoting food management domestically, having obtained certifications such as HACCP, ISO22000, ISO14001.
Since food production is labor-intensive, it is prone to quality impacts caused by worker fatigue. Additionally, the production lines often have unclear records of production quantities, processes, and timing. This obscurity in traceability makes it difficult to track production information when defects occur, leading to food safety management gaps that result in the scrapping of entire batches.
To address this, the Production Development Center at National Sun Yat-sen University utilized its advisory resources to help the food manufacturer tackle food safety management challenges, planning the use of AI technology to collect production data and establish anti-fraud and traceability for food production.
Intelligent manufacturing boosts food safety
Although the level of automation is not high in the processing of bakery products, the food plant in this case is keen to enhance the automation of its production lines and introduce smart manufacturing. For businesses, a traceability system not only helps establish brand image and increase product and brand value, but also gives consumers peace of mind due to the transparency of production lines.
Therefore, the Production Development Center at National Sun Yat-sen University matched AI technology service providers, Hong Ge Technology, in the first phase to plan the introduction of data collection devices to link food work orders information, reducing human operational omissions and capturing real-time production information through dashboards to ensure the consistency of production stage information potentially affected by human factors.

▲ Schematic for intelligent production line planning
The second phase involves using deep learning during the dough fermentation stage to calculate size and volume, analyze the relationship between temperature, humidity, fermentation time, and product volume, and assess whether to introduce AOI foreign object detection after freezing as a second quality control step.
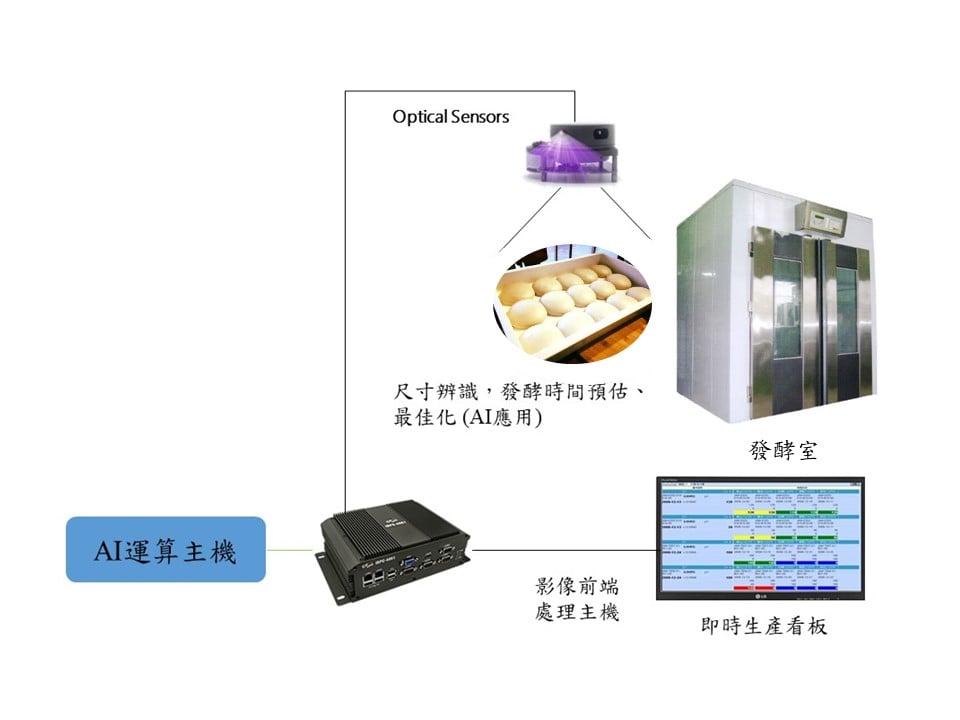
▲ Schematic of AI-integrated quality control for finished products
Food processing ID card, launching the AI-era of food safety tracing
In Taiwan, the understanding and acceptance of production history by consumers is gradually improving. From the supply of raw materials, processing, production, to distribution and sales, it is necessary to have complete control and provide transparent information. Publicly disclosing the production history not only increases trust between enterprises and consumers, but also aligns Taiwan's food safety environment with international standards.
In 2020, the Production Development Center at National Sun Yat-sen University will assist enterprises with the adoption of advanced AI technology, documenting the entire data process from industry to dining table and supervising food production processes to successfully implement product tracing, prevention of adulteration, and the establishment of high standards for products, thus advancing food processing products to international standards.
「Translated content is generated by ChatGPT and is for reference only. Translation date:2024-05-19」