【2020 Solutions】 The First Mask Vending Machine in Taiwan Launched! Yeasan Technology Got You Covered!
Taiwan's "mask prevention" strategy in response to COVID-19 has been effective, resulting in the world’s lowest rate of confirmed cases and lowest mortality rates. Yallvend Tech built the first mask vending machine with an interactive screen in Taiwan. It is equipped with mobile payment, returns transaction data, and manages inventory data. It is an embodiment of Taiwan's "epidemic prevention technology."
Yallvend Tech's core service was originally to provide vending machine manufacturers with networking equipment, platform construction, and other vending machine upgrade services. The Central Epidemic Command Center began implementing name-based mask sales on February 6, 2020 to prevent the spread of COVID-19. In February, Yallvend Tech displayed its mask vending machine technology at Ningxia Night Market in Taipei City. It combines facial recognition and blockchain traceability technology in the first smart mask vending machine, which provided 2,000 non-medical masks for free in just one week, benefiting a total of 1,000 people.
Smart name-based mask vending machine in 6 district health centers in Taipei City, completing transactions online
In order to alleviate the queues at pharmacies, a tripartite meeting between the Ministry of Science and Technology, Taipei City Government, and Yallvend Tech reached the decision to place vending machines in the health centers of 6 districts, namely Xinyi District, Wenshan District, Wanhua District, Zhongshan District, Datong District, and Neihu District, one vending machine each. Citizens only need to insert their national health insurance card to verify their identity, and then use mobile payment, including Easy Card, Line Pay, Google Pay, or JKOPay, to complete the payment.
In addition to using mobile payment, Yallvend Tech has also installed simple POS machines in six other health centers, where citizens can quickly swipe their card, make payment, and collect masks at the mask counter. Each health center distributes 200 masks every day for the public to purchase.
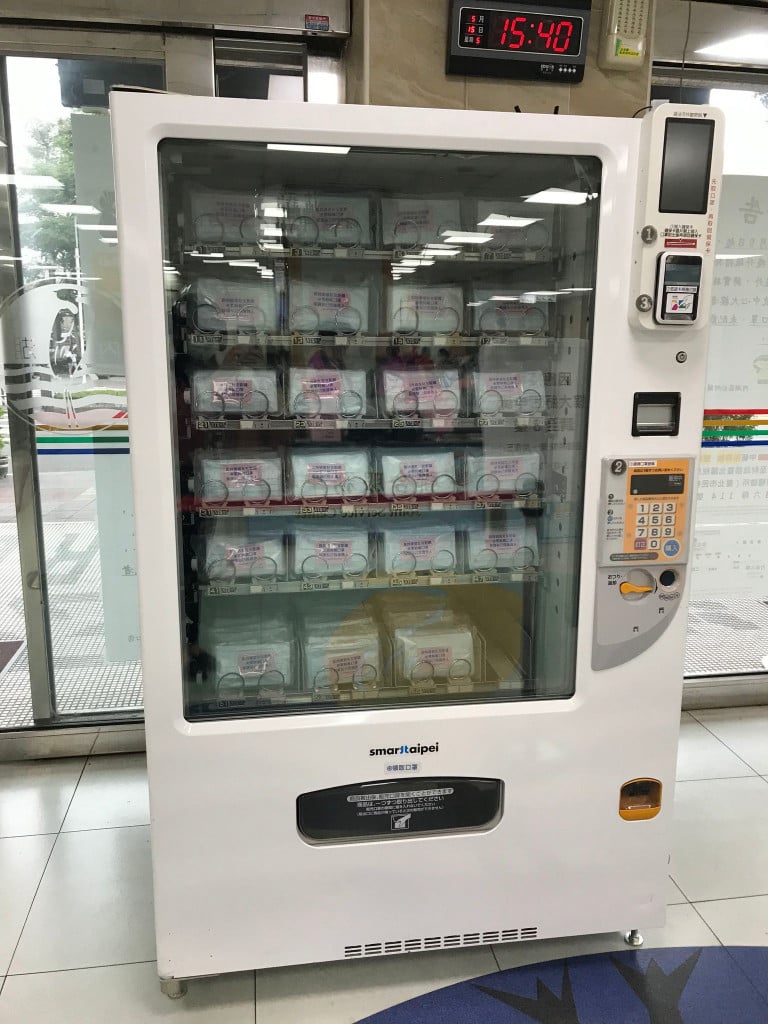
▲The mask vending machine makes it simple and convenient to purchase masks, easily preventing the spread of COVID-19
This time, Yallvend Tech cooperated with Taipei City Government and the Central Epidemic Command Center, successfully gained the support of the Ministry of Health and Welfare's open data database, and paired it with the AIoT human-machine interactive display interface from a well-known e-sports display technology company, so that people no longer need to wait in line and instead use their national health insurance card and online payment to buy masks directly at the vending machine. However, this activity will come to an end in July after the epidemic subsides, and the National Health Insurance Administration's open data API may be terminated by then. Interfacing with the largest and most important health insurance system in the country is a dream project for many engineers. Yallvend Tech completed the connection, testing, and launch in just 12 hours, laying the foundation for the subsequent name-based mask system 3.0. This was a major technological breakthrough by Yallvend Tech.
Founded in January 2019, Yallvend Tech has been deeply involved in vending machine upgrade services. The vending machines we generally see all sell drinks. Yallvend Tech provides the technology that has upgraded vending machines to sell tobacco and alcohol overseas and masks in Taiwan.
Yallvend Tech has identified the needs of the Southeast Asian market and actively invested in the development of core technologies, such as physical identity digitization, online payment, and consumer feature identification mechanisms. It not only attracted attention from major manufacturers such as Coca-Cola at the U.S. Consumer Electronics Show (CES) in 2019, but also opened up the international market.
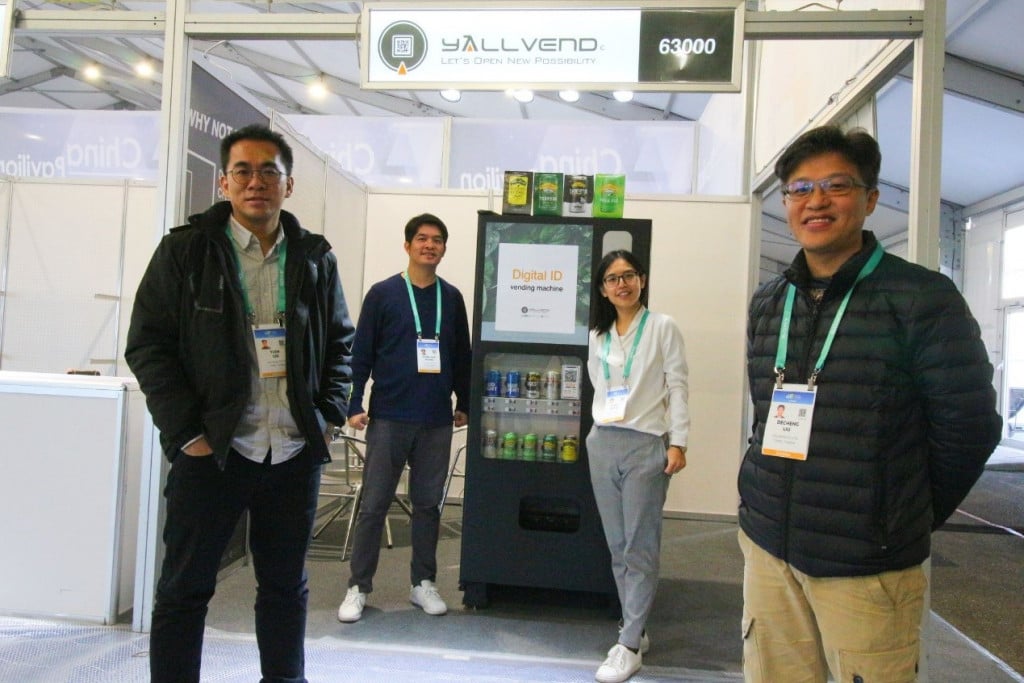
▲Yallvend Tech Team showcases technologies at the CES
For example, alcohol accounts for the highest percentage in the beverage market, but due to the regulations of each country and its physical effect on consumers, many countries will restrict the age for purchasing alcohol, and the same goes for cigarettes. By digitizing identity, smart vending machines will be able to verify the buyer's identity, and buyers who do not meet age requirements will be automatically filtered out. Buyers who meet the requirement can freely purchase tobacco, alcohol, and other products on the vending machines. At present, Yallvend Tech has exported vending machine upgrade solutions that combine identity verification, mobile payment, return transaction data, and inventory data management systems to the Philippines, Singapore, Malaysia, Japan, and Indonesia.
▲Yallvend Tech's product VUK is installed in vending machines on Kokusai Dori in Okinawa, Japan
Two major food and beverage leaders adopt smart vending machine systems
In Taiwan, Yallvend Tech's smart vending machine system was installed in 700 vending machines nationwide by the two leading domestic food and beverage companies. Currently, the vending machines of these two major manufacturers are available in 30% of places close to consumers in factories, offices, and campuses, and real-time promotions will be launched for these vending machines in the future.
In another aspect, Yallvend Tech is also actively developing AI replenishment planning solutions for major beverage companies, hoping to use vending machine data to assist replenishment personnel with replenishing items, route planning, and more efficiently understanding inventory. The company expects to launch related services in about a year.
Recommend Cases
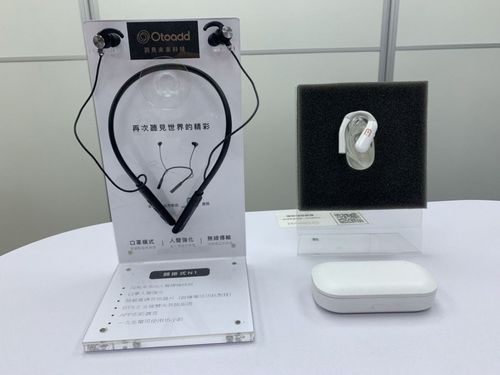
One rainy Thursday afternoon near Taipei Arena, the Taipei Experience Center of RelaJet was fully booked with appointments from people with hearing loss eager to try hearing aids made with a voice separation engine For the hearing impaired, having affordable, lightweight, and effective noise-reducing hearing aids is truly a blessing 'We hope to help users in need to hear the world's wonders again' This empathetic expectation by RelaJet's founder and CEO Po-Ju Chen, who is also hearing impaired, illustrates his understanding of the needs of the hearing impaired He hopes that RelaJet's unique voice amplification hearing aid technology will benefit many more people Affordable hearing aids benefit many with hearing loss Founded in 2018 by Po-Ju Chen and his brother Yu-Ren Chen, RelaJet developed a multi-voice separation engine paired with Qualcomm's Bluetooth audio platform, drastically reducing the price of imported hearing aids, typically costing 80,000-100,000 NT dollars, to just under 10,000 NT dollars They aim to develop affordable goods with excellent noise-cancelling capabilities that wirelessly connect to smartphones In its first two years, the company primarily developed the multi-voice separation engine, which significantly improved the noise reduction quality Once equipped with Qualcomm Bluetooth earphone chips, the audio processing time is drastically short, at about 7 milliseconds to enhance main voice projection and reduce ambient noise, less than half the time required by traditional medical standard of 16 milliseconds for hearing aids, nearly 'zero-delay' 洞見未來科技推出平價助輔聽器,大大嘉惠聽損者 Yu-Ren Chen explains that the primary use of Qualcomm chips for edge computing, along with a streamlined algorithm, achieves extremely low latency and better noise reduction The hearing aids can cover 18 channels, whereas traditional hearing aids cover 4-48 channels In the future, RelaJet will progressively increase the number of channels According to statistics, there are 470 million people globally with hearing disabilities, with a 30 average device use rate in developed countries, with the highest in Western countries Taiwan has nearly 15 million people with disabling hearing loss, of which the middle-aged and elderly make up 30, yet the device use rate is only about 10, which is quite low Yu-Ren Chen further analyzes that the low device usage rate is due to two reasons firstly, the high average selling price of international big brands ranges from 80,000 to 200,000 NT dollars with a three-year usability period, which deters many due to the high cost and maintenance Secondly, in noisy environments, the noise is also amplified which does not necessarily ensure clarity for the users, and the sound parameters can't be adjusted in real-time, making it inconvenient to frequently visit stores for tuning Thirdly, most models cannot connect to smartphones, making it inconvenient for the hearing impaired to take phone calls Utilizing Qualcomm Bluetooth chips for rapid product development In light of this, Po-Ju Chen, formerly a semiconductor engineer at MediaTek, leads the technical development, while Yu-Ren Chen, with a legal background, manages the operations Their seamless collaboration, along with their team employing AI algorithms and chip integration, learns from thousands of hours of audio files in databases through neural networks and deep learning technologies to develop low-latency, high-noise-reduction voice amplification technologies for hearing aids In 2019, this sound processing technology was integrated into Qualcomm Bluetooth chips, winning first place in the Qualcomm Taiwan Startup Competition and becoming a partner in Qualcomm's Global Expansion Program, significantly boosting product development pace In 2021, they launched their own Otoadd series of hearingenhancement products in Taiwan, which received both market favor and positive reviews from many with hearing loss Based on different consumer needs, various product designs are available According to Yu-Ren Chen, the Otoadd wireless earphones with hearing enhancement functions, model N1, are entry-level neckband style priced at 9,500 NT per pair Users can wear the hearing aid while taking calls, and control noise reduction strength and volume through a mobile app They plan to develop accessories in the future tailored to the needs of older adults Besides being available for trials at experience centers in Taipei and Kaohsiung, this hearing aid is also sold through PChome, Taiwan Mobile's myfone, and Elder Age networks, among other channels Another model intended for individuals with mild to severe hearing loss is the Classic R hearing aid, which received the Japanese Good Design Award in 2021 Since its market debut last year, it has attracted those with congenital hearing loss, with users noting improved clarity in noisy environments and appreciating the convenience of Bluetooth connectivity for calls and watching videos This product is anticipated to be exported to international markets in the latter half of this year Additionally, a hearing aid product combining Bluetooth functionality, set to launch in June this year, is sized like typical Bluetooth earphones, targeting visually conscious consumers with hearing loss Its small size and attractive wireless earphone design allow for phone calls, and if approved by the Ministry of Health and Welfare, eligible users can apply for government subsidies RelaJet to expand into overseas markets, using the USA as a beachhead An interesting question arises due to the pandemic everyone must wear masks which impedes lip-reading How does this affect those with hearing loss Yu-Ren Chen indicates that this situation highlights RelaJet's advantages As each person with hearing loss has different levels of hearing ability, hearing aids can only augment to an appropriate volume, assisting users to hear about 60-70 content, with the remainder relying on lip reading and gestures During the pandemic, as everyone wears masks, masks also muffle sounds, but RelaJet's voice separation engine can correct and strengthen the separation, making it easier for those with hearing loss to recognize voices Besides the Taiwan market, RelaJet's next stage will be expanding into overseas markets, expecting to obtain ISO 13485 medical device quality management system certification and US medical device approval in 2022 They plan to enter the US market, either under their own brand or through OEM arrangements Apart from the Taiwan market, RelaJet will also enter the US market in the next phase for hearing aids「Translated content is generated by ChatGPT and is for reference only Translation date:2024-05-19」
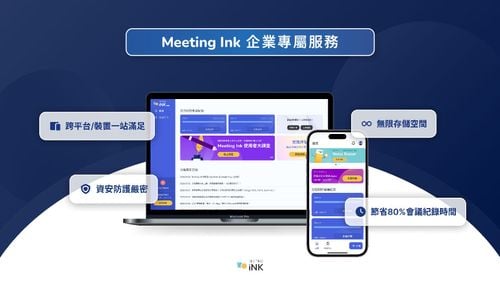
Meeting Ink Enterprise Edition is now being launched Studies show that around 50 of content is forgotten within two hours after a meeting if not tracked and reviewed immediately multiple reports and transmissions can result in losing over one-third of key information Precise meeting records are crucial for organizations with strict operational protocols and public sectors However, with extensive meeting demands, recording can lead to losses in meeting outcomes and increase team burdens Spotting this market pain point, Taiwanese AI startup DeepWave has introduced 'Meeting Ink'—a new solution for meeting records that integrates voice, text, and automated AI technologies Meeting Ink supports voice-to-text transcription, speaker recognition, verbatim translation, and automated meeting summary highlights, offering flexible services for consumers and enterprises This year, it has added real-time verbatim scripting and translation, creating a new paradigm in meeting management AI Technology Solves Meeting Recording Pain Points in One Go Since its launch at the end of 2023, 'Meeting Ink' has become a high-efficiency and accurate meeting record management solution on the market DeepWave combines its proprietary technology, third-party tools, and Microsoft Azure's voice recognition technology to create the best voice-to-text experience Furthermore, this includes speaker recognition and segmenting, multiple language translation, and meeting summary functionalities across various scenarios To achieve broader applications, Meeting Ink also provides real-time application solutions, making it suitable not just for regular meetings but also for events, forums, and educational sessions Currently, Meeting Ink supports both app and web platforms, offering enterprise customization options to expand its applications further Excellent Voice Recognition Technology and Optimal User Experience Meeting Ink stands out in the market due to its precise voice recognition technology and user-centered application design Relying on DeepWave's proprietary technology, Meeting Ink can convert audio signals into text representing each speaker, distinguishing each participant's voice to ensure information is clearly differentiated Additionally, meeting content can be further summarized according to the speaker and, with DeepWave's optimized system, generate exclusive summary templates for various scenes and roles Whether for executive meetings, academic forums, personal interviews, or learning sessions, Meeting Ink produces tailored summaries for different contexts, bringing higher efficiency and flexibility to meeting recording experiences Precisely Targeting Enterprise Needs, Providing Comprehensive Enterprise Applications Anticipating the shifting market demands, DeepWave has launched a customized service plan tailored for B2B frameworks, further optimizing Meeting Ink's application on the enterprise side Enterprise clients can use the professional edition and enjoy exclusive customized summary modules tailored to specific industry needs DeepWave commits to regularly updating AI modules to ensure the most advanced technological support Additionally, Meeting Ink's enterprise service plan emphasizes data security, account permission management, unlimited storage space, and multi-device compatibility supporting all recording scenarios Offered at the lowest market rates, this provides an economical and efficient solution for enterprises, allowing them to focus on core tasks and enhancing overall meeting efficiency Embracing the Pulse of the AI Era, Leading Market Applications According to a 2023 market report, the global market for AI application tools is expected to grow from nearly 7 billion to 50 billion over the next decade, with business and learning tools playing key roles Facing the rapid progression of AI technology, DeepWave leverages its technical prowess and innovative capacity to penetrate international markets with Meeting Ink, continually bringing revolutionary changes to meeting records for both businesses and individuals Going forward, DeepWave will continuously optimize Meeting Ink, committed to promoting the close integration of AI technology with everyday work and learning scenarios, creating more convenient and efficient working environments for users 「Translated content is generated by ChatGPT and is for reference only Translation date:2024-11-15」
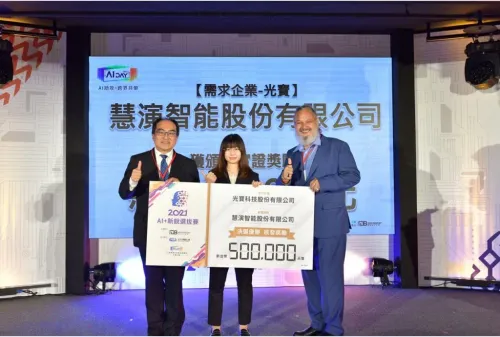
In response to customer demand on a wide variety of products in small quantities in the manufacturing industry, there is an urgent need to find AI solutions from the cloud to terminals Claireye Intelligence provides a solution that integrates software and hardware - BailAI image inspection solution to assist traditional manufacturing industries in improving process efficiency and product quality, thereby achieving the initial goal of transformation After the government declared 2017 to be Taiwan's "First Year of AI," AI startups have sprung up in Taiwan Established in 2018, Claireye Intelligence targets smart manufacturing and provides a platform for AI image analysis and process optimization, using the power of deep learning to detect product defects and abnormalities in the assembly process It assists companies in building infrastructure from terminals to the cloud, which enables automated monitoring of factory production to improve process efficiency and quality Focusing on AI image inspection based on its familiarity with the production line quality control process Shirley Liu, founder and CEO of Claireye Intelligence, is a young entrepreneur She entered the manufacturing industry after graduating from college and held a quality control position in the plastic injection process of hard disk parts "She was already on the production line at the time, and is familiar with the production line process of production machinery" She later switched career paths to marketing and planning, and then worked as an AI product manager When the time came, Shirley Liu decided to start a business, focusing on AI image recognition in the manufacturing industry "The difficulty for enterprises is the lack of an AI development team Even if an enterprise has an AI team, development projects will take a lot of time, at least 6-12 months" said Shirley Liu, who is well versed in the market's pain points The problem that needs to be solved by platforms is to provide services that allow traditional manufacturing industries to build their own AI models without needing employees with a programming background, and to remotely assist production lines with troubleshooting and subsequent system maintenance, helping companies save development time and labor costs BailAI image inspection platform usage scenarios Facing the large number of competitors that provide AI image recognition in the market, what are the technical advantages of Claireye Intelligence Shirley Liu said that many companies currently have AOI equipment, but the bottleneck in the application of AOI is that it can only be used for defect inspection in fast production of large quantities, and parameters need to be adjusted after each inspection or production Based on her understanding of the industry, most SMEs are limited by their financial resources due to AOI equipment often costing over NT1 million, but they also want to use automated inspection This is where Claireye Intelligence comes in Shirley Liu went on to say that it is impossible for traditional manufacturing industries to maintain a technical team that includes AI engineers, data engineers, cloud architects, and terminal architects Claireye Intelligence specializes in software and hardware integration Enterprises can use the BailAI image inspection platform to easily solve inspection problems on the production line In other words, customers only need to provide images or samples for Claireye Intelligence to carry out model training, model deployment, and system integration, and they can easily use AI technology to optimize and monitor production line processes Participated in the AI New Talent Selection and achieved a recognition rate of over 90 in assembly behavioral image recognition For example, a certain connector manufacturer only has 1-2 AI engineers in its technical team The main problem that needs to be solved is that most operators are on the production line, while quality control and senior managers are not on site, and the company wants to understand the actual situation of the production line through remote monitoring Claireye Intelligence uses industrial cameras to capture production line images, and transmits AI image analysis to the remote end Supervisors and quality control personnel can observe if there are any errors in the production line assembly, such as whether the connectors and lines are connected properly, through the monitor Claireye Intelligence's AI image inspection operates on Microsoft's Azure cloud platform, and also utilizes terminal equipment, such as NVIDIA's edge computing equipment placed around the inspection station, to assist traditional manufacturing industries with improving production line efficiency and detecting problems early through an integrated solution from the cloud to terminals Claireye Intelligencersquos customers currently include aviation, electronic peripherals, connectors, and metal industries Assembly process solution for human behavior recognition in assembly lines achieves an accuracy of over 90 In order to demonstrate the depth of technology, Claireye Intelligence participated in the 2021 AI New Talents Selection of the Industrial Development Bureau, Ministry of Economic Affairs, and provided Lite-On Technology with the "assembly process solution for human behavior recognition in assembly lines" The solution determines effective working hours and ineffective working hours of operators on the production line through cameras and AI image recognition It recognizes hand posture and position through images to determine the operator's assembly behavior, achieving an accuracy of over 90 Shirley Liu added that the assembly process of electronic components is complex, mostly carried out manually, and cannot be replaced by robotic arms Claireye Intelligence used cameras to film the assembly process of operators at Lite-On's assembly station The algorithm is then trained and corrected based on the video, and the final trained model can directly determine whether there are any errors in the assembly process to improve the overall process Project development time is expected to be shortened to 1 month by using the BailAI image inspection platform Since its establishment more than three years ago, Claireye Intelligence has accumulated a considerable amount of project experience and hopes to commercialize the project experience Shirley Liu pointed out that the trial version of BailAI image inspection will be completed this year 2022 Customers can choose industrial cameras or video cameras based on the detail of the object being inspected It can even use X-rays to capture images, and then the images are automatically marked by the platform Claireye Intelligence will provide customers with AI application models suitable for the field Inferences can also be made in the cloud or terminals for launch in the manufacturing industry The metals industry, metal casings of industrial computers, connectors, electronic peripherals, and mechanical parts can all use the platform for defect detection and object identification Claireye Intelligence will continue to improve its technical capabilities, accumulate customer experience to complete commercialization, and also accelerate the implementation of AI inspection applications In the mid-term, it will build terminal and cloud infrastructure and shorten the development time of enterprise AI projects from 6-12 months to 1 month, reducing usage time and lowering the threshold for enterprises The long-term goal is to target the Southeast Asian market where Taiwanese businesses are gathered, expand software and hardware integrated AI solutions to overseas markets, and expand the scale of operations