【2021 Application Example】 Hamastar Technology Builds an AI Model Management Platform to Accelerate the Application of AI

Riding the AI hype train, financial service providers are using their solid foundation in the industry to not only transform themselves, but also assist their customers with transformation!
Hamastar Technology, which has been established for over two decades, has been developing AI technology and assisting industry customers with the implementation of AI in recent years. Hamastar Technology believes that to implement a complete AI project, in addition to AI theoretical knowledge, data analysis, and model training capabilities, it is also necessary to develop APIs for data, establish databases, develop front-end RWD web pages, and even consider layout design and user experience based on customer needs. These tasks create technical barriers for AI startups. Even from the perspective of companies that have reached a certain scale, it is hard to accumulate technical experience and accelerate business growth due repeatedly investing manpower developing similar functions in each project.
Institutional customers still require high level of customization for AI
Using the requirements of government Agency A implemented by Hamastar Technology as an example, users must control false information from specific channels. The platform needs to provide data ingestion functions for training models and predictions, and can complete natural language processing (NLP) text classification model training and use. When the model discovers false information, it needs to immediately notify responsible personnel through messaging software. The need of Agency B is to use an AI model to automatically classify petitions and immediately provide information on past cases as reference for the petitioner or officer. Although the project models are similar (data ingestion, model prediction, warning / notification), the required functions still need to be separately developed for individual projects, and existing programs and models cannot be reused to speed up the implementation of subsequent projects.
After in-depth discussion, Hamastar Technology found that pain points of enterprises implementing AI projects include high implementation costs and lengthy project schedules. It is difficult for a single enterprise to simultaneously have data scientists, analysts, engineers, and designers. Current projects are all focused on solving the needs of specific fields, and it is difficult to reuse the AI models in other fields of application. At the same time, the tools are concentrated in AI projects and cannot provide customers with total solutions.
In other words, due to the "limited manpower," "restricted fields," and "insufficient tools" of AI service providers, the implementation of AI technology projects requires high costs or lengthy timelines. These are common problems that companies urgently need to solve. Therefore, if there is an AI model application service management platform, it will be able to solve the above difficulties and not only reduce costs, but also accelerate project implementation and provide customers with one-stop solutions.
AI model application service management platform assists in quickly completing projects
Therefore, with the support of the AI project of the Industrial Development Bureau, Ministry of Economic Affairs, Hamastar Technology carried out the "AI Model Application Service Management Platform (AISP) R&D Project" and engaged in the R&D of AISP products. The purpose is for AI service providers to complete the AI projects with twice the result using only half the effort.
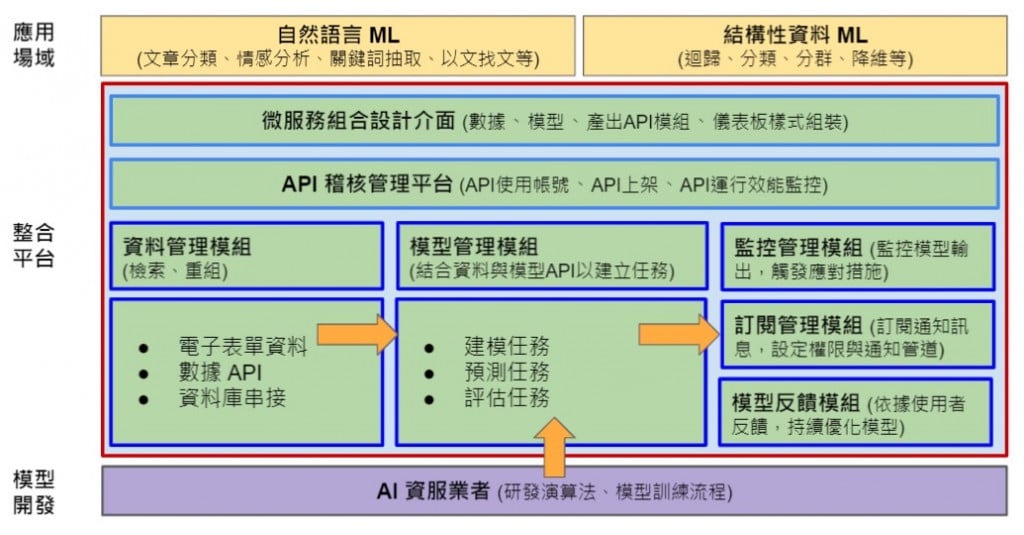
▲The AISP provides one-stop AI solutions
AI service providers can quickly assemble required functions, such as data API, model management, and model prediction result monitoring / subscription through existing module functions of the AISP. It also provides commonly used graphical tools to help companies quickly design interactive charts or dashboards required by users, effectively reducing the labor costs required to execute projects, shortening the solution POC or implementation time, and accelerating the implementation and diffusion of industry AI.
In terms of product business model, in the short term, the company will extensively invite IT service providers with expertise in the field of AI to work together, and use platform services to solve the AI implementation problems faced by requesting units in various field, gradually building trust in the platform brand. In the mid-term, the company hopes to gradually expand the market based on its past success, and form strategic alliances with multiple IT service providers to solve more and wider problems in specialized fields and provide more solutions for units to choose from.
The platform combines field experts to jointly expand overseas markets
In the long term, after establishing AI strategic alliances in various specialized fields, the platform will have a large number of AI solution experts for specialized fields. After accumulating a large amount of successful project experience, Hamastar Technology hopes that the AISP will be able to work with experts / companies to expand into the international market.
Harmastar Technology Co., Ltd. was formed in 2000 by recruiting numerous senior professional managers and technical experts in related fields. It is committed to software technology R&D and services, and aims to develop into an international software company, actively creating opportunities for international cooperation in the industry. Under the excellent leadership of its first president, the company has rapidly grown into a major software company in Taiwan.