【2022 Solutions】 Xiaoshi Intelligent Inspection uses the two swords of "AOI + AI" to combine software and hardware to open up the two channels of appearance defect detection and supervision.

Quality inspection, like a double-edged sword, has always been a favorite and painful subject for Taiwanese manufacturers. When AI deep learning enters the industrial visual inspection of traditional manufacturing industries, it can not only save inspection manpower investment, solve the problem of inconsistent manual visual standards, overcome the limited visual recognition and defect detection blind spots of traditional automatic optical inspection (AOI), and also enable real-time traceability Causes of quality problems. The overall AI+AOI visual inspection solution developed by Xiaoshi Intelligent Inspection integrates software and hardware to create efficient appearance defect detection capabilities, helping electronics OEM customers create high-efficiency products with a miss detection rate of less than 1% and an overkill rate of less than 3%. Check the level.
Xiaoshi Intelligent Inspection was established in 2020. Although it is a new venture two years ago, it did not start from scratch. Founder and CEO Hong Peijun and the core team have been deeply involved in Foxconn factories for many years and participated in countless smart factory-related solutions and process improvements. , has profound AI deep learning development capabilities, and accumulated rich experience in world-class AI application implementation. Seeing that AI industrial inspection must be the last mile for the manufacturing industry to move towards Industry 4.0, Hong Peijun resolutely decided to implement AI deep learning technology in the field of smart manufacturing with high output value, and specialized in the development of AI industrial visual inspection.
For the manufacturing industry, product inspection is the most important part of all quality control, but traditional industrial inspection faces two major pain points: 1. Manual visual inspection: Today, more than 95% of the entire manufacturing industry still relies on manual visual inspection. Inspection makes it difficult for manual visual quality inspection standards to be consistent, and visual inspection of fine objects, such as passive components or highly reflective components, will cause long-term vision damage. 2. Traditional AOI automatic optical inspection: The product has limited visual recognition capabilities and blind spots in defect detection. Among them, the detection of appearance defects such as scratches, oil stains, dirt or hair and other unexpected subtle defects has always been a problem in AOI applications. Insurmountable difficulties.
AI+AOI visual inspection overall solution is a great boon for appearance defect detection
When designing the product roadmap of Xiaoshi Zhikan, customer group positioning and strengthening customer product services and value were important indicators. Moreover, appearance defect detection has always been an unresolved pain in the manufacturing industry, Hong Peijun said. With industrial quality inspection AI software as the core, Xiaoshi Intelligent Inspection provides an overall solution for AI+AOI visual inspection. It mainly promotes three major products, including "QVI-T AI deep learning inspection modeling platform software" and "AI six-sided defect inspection and screening machine". ” and “AI Industrial Quality Inspection Platform”. The main customer groups served are semiconductor packaging and testing, EMS electronics foundry, small metal parts processing and other industries with high production capacity and high gross profit margin. In response to customer needs, Xiaoshi Intelligent Inspection provides corresponding software and hardware services, combining self-developed AI deep learning software and hardware quality inspection equipment to reduce the manual visual burden on the production line and effectively improve the production quality of the factory.
In order to help equipment manufacturers and technical engineers with development capabilities accurately grasp product appearance defect detection, Xiaoshi Intelligent Inspection independently developed QVI-T deep learning detection software, which can provide customers with defect location, defect classification, defect segmentation, anomaly detection and text recognition. Key functions such as this are different from the fixed detection methods of traditional software. Algorithms can be refined based on different industrial detection methods and different APIs can be developed to connect devices with different lenses. The software design of this platform is very lightweight. It is a SaaS software built on public cloud/private cloud. It mainly involves simple image uploading, labeling, training modeling, and verification testing. After completion, users can download models, SDKs, APIs, and reports. Effectively help customers achieve AI inference functions.
Currently, most of the industrial inspection services on the market are traditional AOI software industrial inspection machines, which can only measure product contours such as the head and length of fasteners, etc., and cannot truly provide detection of subtle product surface defects such as screw head cracks and tooth damage. There is a lack of such high-precision defect detection companies in the market, Hong Peijun observed. Xiaoshi Intelligent Inspection developed and independently built the "AI six-sided defect detection and screening machine" from customized services in the past to providing standardized services for customers at the current stage. It provides standardized testing services for fasteners in measurement and surface defects, as well as passive components. High-speed surface defect detection of similar products. This professional machine uses the AI deep learning + AOI composite algorithm technology independently developed by Xiaoshi Intelligent Inspection. Through parallel computing technology, it can achieve model inference up to 3 milliseconds per picture, and realize multiple complex defect detection on the electrodes and body of passive components. This professional machine is mainly used for the inspection of fasteners, small metal parts and passive components.
In terms of competitiveness in the industry, the software + hardware integration provided by the AI six-sided defect inspection and screening professional machine is an important core competitive advantage of Xiaoshi Intelligent Inspection. It is not as simple as it sounds. Hong Peijun said with emotion that this special machine is very important in the industrial inspection industry. Commonly known as the highly integrated integration of optical mechanisms, electronic controls, software and algorithms, the process requires continuous optimization and iteration, and requires multiple client verifications and modifications. After a long period of hard work, the technical threshold has also been raised. The AI six-sided defect detection and screening professional machine will be the main product promotion direction of Xiaoshi Intelligent Inspection in the next 3-5 years. It is believed that AI combined with measurement technology and surface defect detection will be an important source of core competitiveness of Xiaoshi Intelligent Inspection, Hong Peijun said.
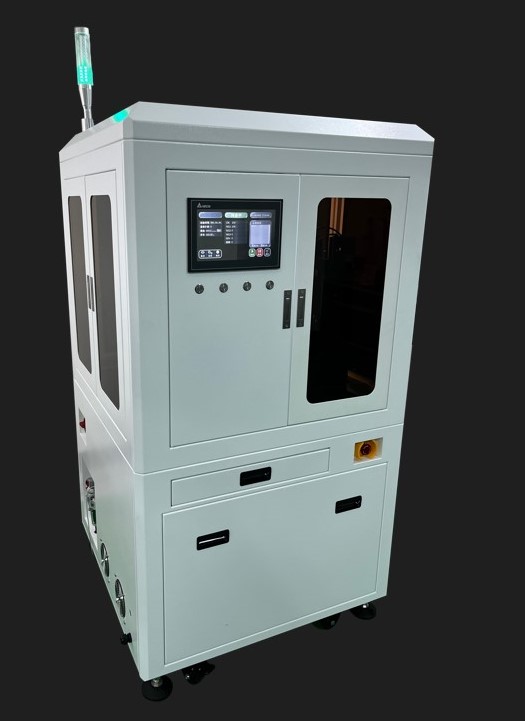
▲AI six-sided defect detection and screening professional machine will be the main product promotion direction of Xiaoshi Intelligent Inspection in the next 3-5 years
Faced with the booming development of Industry 4.0 in smart factories, customers often ask "Does quality inspection data have secondary use value?" Hong Peijun said that the "AI Industrial Quality Inspection Platform" launched by Xiaoshi Intelligent Inspection has a machine learning mechanism , which can be used for secondary use of quality inspection data to provide customers with multiple functions including real-time monitoring and early warning of production quality, quality traceability analysis, quality factor assessment, process parameter prediction and recommendation. Taking the successful introduction into the automotive parts factory as an example, through the prediction and recommendation of process parameters provided by the AI industrial quality inspection platform, when we know the product defects, we build a set of models based on the experience of past masters, coupled with the network connection data from the previous stage, After integration, we have process data, incoming material data, and quality inspection data. We can predict whether these machine parameters have run out, and we can recommend whether the process parameters of certain sections should be adjusted up or down. Through the AI industrial quality inspection platform, Xiaoshi Intelligent Inspection can help customers connect visual quality inspection results, process data and acceptance standards with the existing MES system of the customer's factory to improve production quality, improve efficiency and reduce costs.
In terms of business model, Xiaoshi Zhiqian also provides a software subscription system for the deep learning detection modeling platform software. It provides public cloud customers with traffic subscription and charges based on the amount of image uploads, while private cloud customers adopt an annual license fee. (license) charging mechanism. In addition, the company also provides customers with a buyout charging mechanism for the overall solution (equipment), and provides a one-year warranty, after which consumables and software update maintenance fees are charged annually.
Going in the opposite direction, using both hard and soft methods, with a missed detection rate of less than 1% and rapid modeling in 15 minutes
Faced with various small-volume and multi-sample inspection needs in the manufacturing industry, general AI deep learning visual inspection usually requires customers to collect a large number of photos of defective products, which is time-consuming to label, and also causes customers to have difficulty in importing AI, and defective products cannot be collected. The introduction cycle is long and implementation is full of risks. If there are not enough bad samples, the model will be inaccurate. Kosaki Chikan goes in the opposite direction and uses its product "AI Visual Inspection Model Development Tool" to train models through pictures of good products provided by customers. It is relatively easy for AI to learn good products, no labeling is required, and the time can be quickly compressed to complete the modeling.
Take the implementation of IPC electronics industry - AAEON Technology as an example. In order to reduce the manpower input of the quality inspection station in the PCBA production line and have standardized quality inspection, Xiaoshi Intelligent Inspection provides an overall solution for PCBA AI visual inspection software and hardware. services, and conduct in-line inspection on the factory's highly automated assembly line, effectively saving inspection manpower investment, improving the standardization of quality inspection rates, and improving the problem of inconsistent standards caused by manual visual inspection. Through the introduction of AI visual inspection software and hardware integrated solutions, we have effectively helped customers maintain an overkill rate of less than 3% in the past two years, and achieved high-efficiency performance with a missed detection rate of less than 1%. In addition, this solution allows practitioners who do not understand AI to quickly operate modeling. By installing the modeling tool on the device, when the customer has a new product number and needs to create a model, he only needs to provide 10 pictures of good products to scan under the device. It only takes 15 minutes to quickly train the model.
In terms of product core strategic layout, compared with market competitors who rely solely on general software services to seize all manufacturing markets, it is not feasible to apply it to industrial inspection. Hong Peijun has observed over the past 10 years and believes that only software + hardware can With technical thresholds and focusing on one industry and field, only by adopting a standardized company's AI six-sided defect detection and screening special machine can it be replicated and scaled up, and the company can truly continue to move towards optimization and create product competitiveness, even if there are other competing products. It’s not easy to compete for this pie, Hong Peijun said.
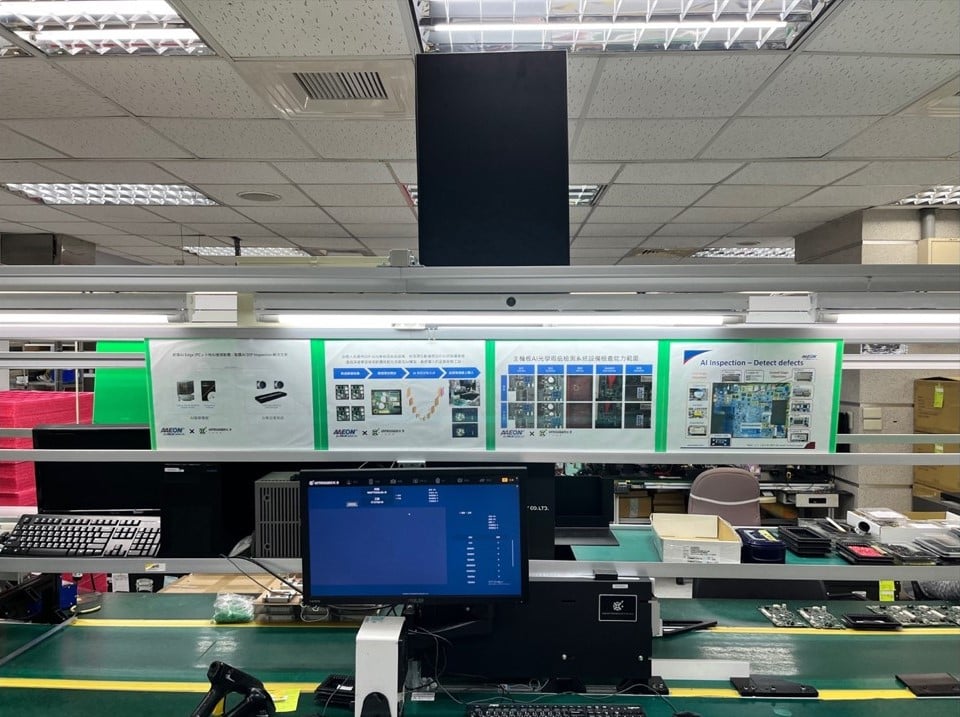
▲Xiaoshi Intelligent Inspection’s overall AI+AOI visual inspection solution creates rapid modeling and excellent results for customers with a missed detection rate of less than 1%
The most competitive AI+AOI overall solution provider with global presence
For new entrepreneurs, facing business expansion is a challenge every day. Hong Peijun said that small companies are easily snatched away by large companies, company talents are poached by high salaries, lack of deep customer relationships, and the business team is not large enough, etc. . How to overcome this? Hong Peijun believes that the key to success and competitiveness of a new start-up company is to be diligent in making up for mistakes, provide better services, provide more immediate feedback, and create more professional solutions to convince customers.
Since its establishment in 2020, Xiaoshi Intelligent Inspection has always gone against the grain in terms of product core strategic layout, surpassing the competitive market among its peers, and actively taking root in the overall solution of AI visual inspection software and hardware. Hong Peijun hopes that Xiaoshi Intelligent Inspection will become the world's most competitive AI+AOI overall solution provider for the electronics and semiconductor industries in the future, and provide the top AI+AOI professional machines and equipment to the electronics and semiconductor industry customer base. Hong Peijun said that the technical capabilities of the company's AI six-sided defect detection and screening professional machine have reached the top domestic level. In order to speed up the research and development of professional machines to become more standardized and sell them to overseas markets, the company will conduct a fundraising plan at this stage, hoping to use legal persons such as the Capital Strategy Council to assist in more business connections and fundraising channels. For the medium and long-term goals, Xiaoshi Intelligent Inspection will lay out the global market including mainland China and Southeast Asian countries. At the same time, it will follow the international footsteps of major OEMs in global layout. Under the target inspection project, it will continue to develop specialty products and spread towards the international field.
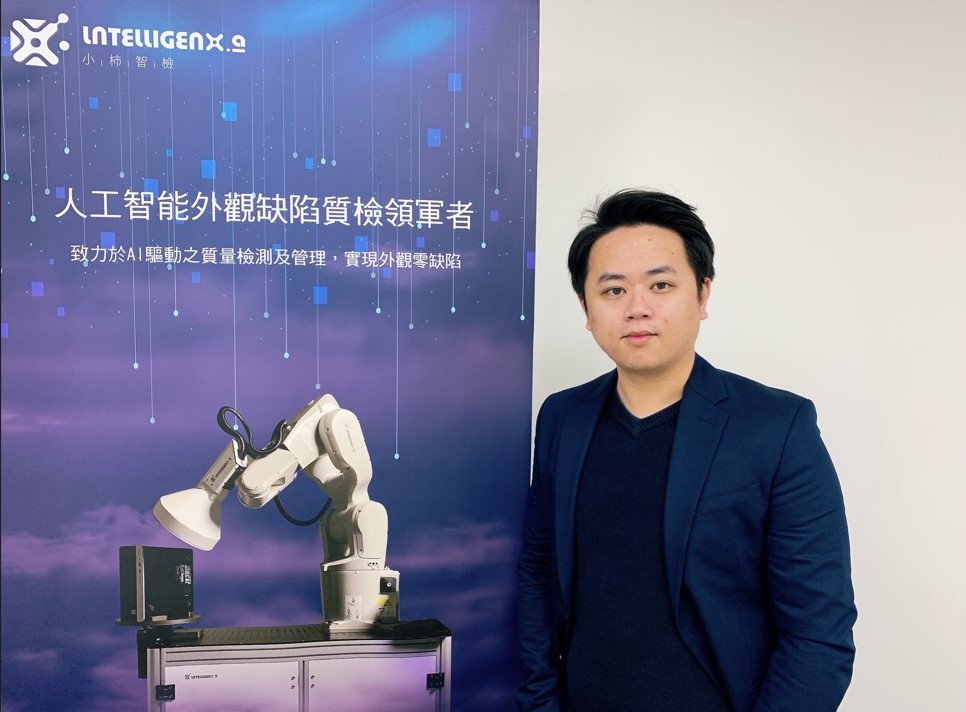
「Translated content is generated by ChatGPT and is for reference only. Translation date:2024-05-19」