【111年 應用案例】 搭上綠能商機 華鉬實業打造全釩液流電池儲能系統設備 長效儲能的最佳選擇

綠能是未來趨勢,必帶動未來龐大商機。而風力發電是近年全球矚目綠色能源之一,將成為我國再生能源重要生力軍、幫助台灣發電量於2025年達到20%的目標,以提高台灣能源自主性。隨著國內風力發電機(風機)組數量和電量逐年增長,如何讓儲電設備達到安全、長效性、充放電不易衰減和永續低碳又環保的技術能量顯得格外重要,同時風機設備本身的健康檢測、保養與維修也成為風場業者關注焦點。為滿足風場客戶需要,華鉬實業旗下綠能事業部門推出長效儲能的全釩液流電池電解液及風機AI預測性運維,提供100%安全、長效性且可降低客戶初製成本的電力儲能設備,並透過AI預測性運維服務協助客戶降低發電度成本10%,節省最多30%維護保修成本。
華鉬實業成立於1998年,本業以提煉釩、鉬及稀有金屬元素等製品起家,並運用於高階鋼鐵、專業化工及特用化學品等行業,而釩更如同煉鋼的維他命可加值煉鋼的成效。其中釩、鉬相關製品為公司主力項目之一,公司看見100%以釩元素為主的全釩液流電池在長效儲能上未來將是相當被看好的綠能技術主流,並且2010年以前政府已積極請法人如工研院在固態電池和全釩電池進行相關零組件材料投入研究,再加上經濟部期許再生能源在2025年發電量佔比達20%目標並達1.5GW,基於上述考量,華鉬實業決定於2017年全力研究與投入自主開發的全釩液流電池電解液的技術開發,以藉此加速2025年再生能源的達標率。
華鉬公司指出「再生能源的電源較不穩定,而台灣本身缺乏鋰資源,在鋰電池製造上幾乎80%-90%電池芯必須倚賴國外採購,缺乏100%國內自足自給的儲能資源與技術。」同樣地,對於本身沒有天然釩礦資源的台灣是如何克服呢? 為此,華鉬實業利用獨創技術,透過石化業如中油煉油廠或台朔石化製程中的廢觸媒,其中有高達10%釩離子成分可提煉出高價值的釩礦資源,藉此生產出台灣100%自主自製的全釩液流電池電解液且不受資源影響,有效達到資源循環再利用。自2017起華鉬實業已成功打造出全釩液流電解液技術,並順利通過工研院和核研所及多家國際大廠的產品驗證。
台灣在儲電能量目標於2025年要達1.5GW,其電力分配包含500MW於台電的自動調頻系統、500MW於E-dReg及500MW於既有或新設的太陽能電廠,以太陽能電廠的用電使用為例,主要以下午4點到晚上10點用為民生用電尖峰時段,為此,能源局特別要求台電必須加強儲能設備的升級,也因此帶動市場上對全釩液流電池儲能系統設備的高度需求。另外,台灣在目前總儲備電能的建置與貢獻尚未達到100MW,距離2025年目標1.5GW儲電量仍差距15倍以上。
運用全釩液流電池 成功打造100%安全、低碳環保又長效性儲能系統設備
相較於鋰電池的短效電力儲能,全釩液流電池的最大優勢為全球公認可長效性的儲備電能,可以長時間儲能達12小時,代表若充12小時電力,則可以釋放12小時電力。相較於一般儲能系統的計電方式也就是每日用電度數=功率(以千瓦為單位) x時間(以小時為單位),對全釩液流電池而言,功率和小時數是各別設計,該功率又稱為電堆,是由金屬、高分子模、碳氈和石墨板等四種材料組成,而該用電時間改以電解液的量(以立方體為單位)來計算,因此當功率(電推) x電解液的量=我們每日運用全釩液流電池儲能的用電度數。
全釩液流電池儲能系統設備之產品特色方面,包含安全性、長效性、充放電不易衰減和永續低碳環保性等四大特色。全釩液流電池品質是100%安全,由於電能是儲存在含釩的電解液中,能避免儲飽電的儲能系統造成任何易燃事故發生。在電池壽命上,相較於鋰電池的電池壽命短暫,全釩液流電池透過價數變化可高達20-25年以上電池壽命。對於儲能的充放電性能,不像鋰電池有一定充放電次數(5000-600次),全釩液流電池的充放電次數是沒有限制性的。對於全球高度重視的零碳排放,不同於鋰電池有回收議題,全釩液流電池的電解液可永久使用,該電堆材料成分是環保的且可完全回收,以打造真正永續性又低碳環保的儲能系統。
陸域風機AI預測智慧運維 讓客戶降低發電度成本10% 省下維護保修成本高達30%
華鉬實業不只透過全釩液流電池儲能系統設備提高再生能源客戶長效儲電效能、協助客戶降低初置成本,更透過離岸與陸域風機AI智慧運維實證計畫在台電的陸域風場的場域實證,積極累積自家在AI預測性運維的技術經驗和能量。在經濟部工業局AI HUB計畫支持下,合作場域將以台電公司路域一期風場為主並提供6個月以上風機的智慧運轉數據進行分析。本次陸域風機的AI預測運維系統,採用機器學習方式,主要技術提供者來自英國British Petroleum(BP)石油集團的子公司ONYX Insight,該公司透過AI Hub分析軟體技術進行台電面臨的風機痛點分析,包含路域風機的發電量損失和陸域風機的關鍵零組件(如齒輪箱、變槳軸承…)在異常震動(三維的振動頻率)或異常溫度等狀態下進行損壞預測等報告產出。透過本次落地實證可有效協助台電降低發電度成本10%,增加資產價值1~2%,節省最多30%維護保修成本。近三年ONYX Insight在全球已成功預測運維2萬台以上離岸或陸域風機,累積極高的AI模型準確率。相信透過與ONYX Insight建立的國際合作夥伴關係,將有效輔導並加速華鉬實業的綠能事業部在邁向成為風機AI預測性運維的獨立科技服務提供者之目標與布局。
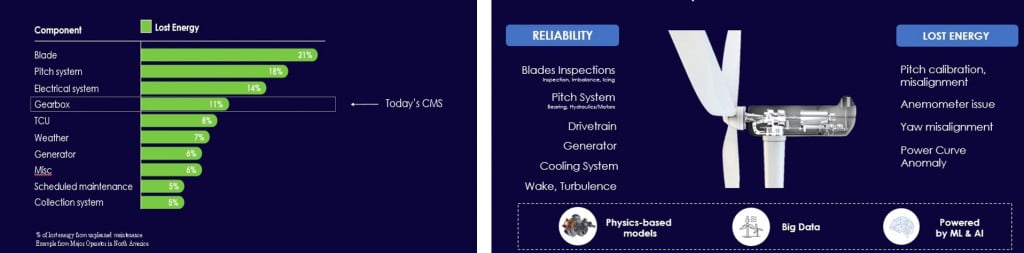
▲與合作夥伴ONYX insight提供客戶AI預測運維系統,包含風機發電量損失與風機關鍵零組件之損壞預測
厚植國內風機運維的基礎 以台灣為基地 拓展到東南亞風場
離岸風機AI預測性運維未來在台灣將超過300億台幣的的市場產值,儲能市場在全球更是有千億美金以上的產值,在未來公司願景,華鉬實業期許能成為釩液流電池電解液及風機AI預測性運維的獨立技術服務提供者。而長期目標,透過累積豐厚技術及實績資本,在世界各地建立釩液流電池電解液之在地供應鏈,就近供應產業需求。