【109年 解決方案】 馬達、風扇靠AI抓異常,華碩AI 解決方案團隊展現特異功能

「風扇」是遍佈在電腦及家電上的關鍵小零件,看似簡單僅屈指可數的部件組裝起來,小歸小,卻是為機器維持「涼爽」而能確保壽命的關鍵元件。但風扇廠如何檢測出組裝品質好壞的風扇呢? 答案是「聽」風扇運轉的聲音判斷良莠,軸心偏移、培林異常、葉片干涉等等會使風扇運轉時產生異音,此一風扇即為組裝不良品,舉凡各類「動件」如馬達、引擎,壓縮機等的組裝品質大多由類似的方式完成組裝品質檢測 (如下圖,聽診檢測福特RS引擎組裝品質)。
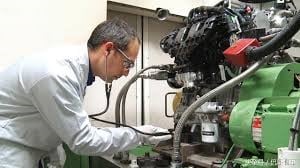
▲聽診檢測福特RS引擎組裝品質(圖片來源:kknews.cc)
一直以來風扇業在品檢員正式上線前,必須先完成3-6個月「聽力辨識」訓練,工作地點在電話亭一般大小的隔音室內,以確保不會有其他環境背景雜音干擾,缺點是6個月左右後(因人而異),人耳會對特定聲音疲乏必須轉任其他工作,華碩智慧解決方案(AI Solution) 團隊利用「人的聽覺敏銳度會隨時間下降,但AI不會」,徹底解決風扇業者必須不斷重新訓練品檢人員的痛點。
AI聽出問題馬達,華碩協助業者品質把關
為解決上述痛點,華碩利用錄製合格風扇的運轉聲音,製作「好的風扇聲音波形」讓AI學習,華碩智慧物聯網事業群共同總經理張權德表示:「這不是比對聲音,比對意味要一模一樣,但對於風扇,AI必須要學習什麼屬於好的一類,什麼屬於異常的一類。」同時,透過華碩的技術,能夠讓訓練、建立AI模型變容易,並且可以讓自己的PE 工程師 (production engineer) 來執行建立AI模型的工作,讓模型留在企業內成為關鍵的核心競爭力,每一個新型號風扇導入生產時,只要錄製3段各30秒的合格風扇的運轉聲音,新型號風扇的AI 模型就建立完成,立即投入生產。國內若干3C風扇生產廠陸續建置華碩智慧波形檢測解決方案,導入時華碩協助訓練並優化AI 模型,已達等同品管員百分之百一致的檢測辨識率,同時開心的表示AI 檢測 1. 可以持續不間斷的工作; 2. 產出的品質一致; 3. 建立產品生產的數位履歷,便於產品追蹤與日後製程分析,這一直是風扇廠長久以來想完成的課題。
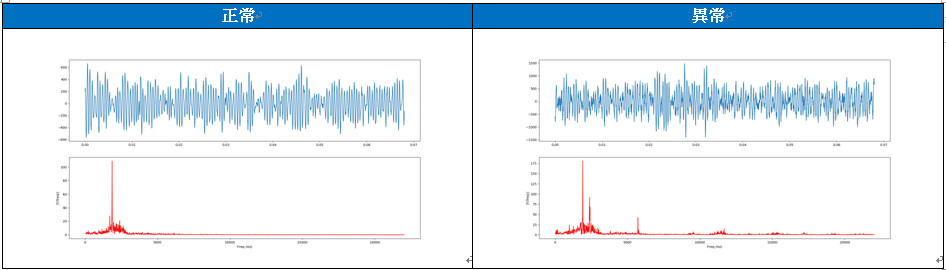
除了熟悉的3C 風扇,華碩AI智慧波形解決方案的聲音異常辨識對所有「動件」都適用, 也能對工廠所生產的馬達做組裝品質檢測,一旦AI「聽」出馬達有不正常的聲音,就能挑出瑕疵馬達。除了聲音之外,同一套人工智慧方案也對電流、電壓及振動波形具有同樣的辨識能力,有些生產場域具有強的背景噪音或者收音不易等原因,可以彈性改以偵測電流、電壓或振動的波形來進行異常的監控,達成產品組裝品質的檢測。
AI認識數位波形,設備預防保養
AI也能「聽」出廠區設備馬達是否有異常,用科學化方法聽出馬達「該保養」或「該替換」。一般廠區馬達都是透過巡查的方式採週期性檢查,對鋼鐵或化工業連續製程而言,一旦馬達中途故障,耗損的是整條產線上的鋼材或原料,是馬達成本的數十倍甚至數百倍,況且大部分馬力稍大的馬達都不是隨訂隨到,意外停機延續數日或數周損失重大,大多利用歲修提前替換馬達,例如馬達原有五年壽命,業主可能二~三年就更換,即使成本變高,也比整條產線材料報廢或停機好。利用華碩智慧波形異常檢測方案對廠區內所有的馬達運作做追蹤,馬達等設備產生運作異常隨即發出警示,從容安排檢修或零部件更換,達到設備預診保養目的。
AI檢測使用便利,佈署快速
生產場域及產品品質檢測的環境場域各有不同,AI應用開發大致都高度客製化,若華碩智慧解決方案團隊必須一件一件針對客戶客製化AI,面對上游零件供應商高達200~300家,產品多樣分散,勢必要消耗極大資源,這樣效率太低,所以「降低客製化比率,提高共同化」是華碩智慧物聯網團隊的另一個目標。期望將業界AI應用客製化比率從60~70%降至20~30%,未來每接到一個專案,華碩智慧物聯方案客製化調整比例只要2成,這樣方案才可以複製並規模化,快速佈署。