【110年 應用案例】 以AI補足傳統產業經驗傳承的斷層 塑料再生製程之產量預測分析

當傳統產業仰賴的老師傅越來越少
在台灣,中小企業一直以來扮演著台灣產業的中堅實力,陪著台灣走過各種「經濟奇蹟」的時代。但隨著時間演進,昔日的師傅也逐漸變成了老師傅,再加上台灣社會的少子化現象,以及整體產業結構的變化,越來越少新一代的年輕人願意進入傳統產業,如今也可以發現,大多中小企業內的機具操作現場,已經由「老師傅」搭配「外籍勞工」的組合形成主流,而身為現場經驗活字典的老師傅們,卻也缺少後續者能夠持續傳承經驗,逐漸產生了傳統產業的現場經驗難以持續傳承的現象。
傳統人工作法優化製程的極限已在眼前
位於台南保安工業區的「唐先企業」,於1972年創立,以製造優質的編織機具設備起家,同時具備有製造機具之實力,也因為近年來隨著響應國際間綠能、再生、環保,唐先企業積極研發塑料環保再生設備,最終以簡約高效的機體設計,輔以先進智慧化的核心控制技術,成功研發出低能耗、低廢料、高純度、高產出的回收製粒設備。
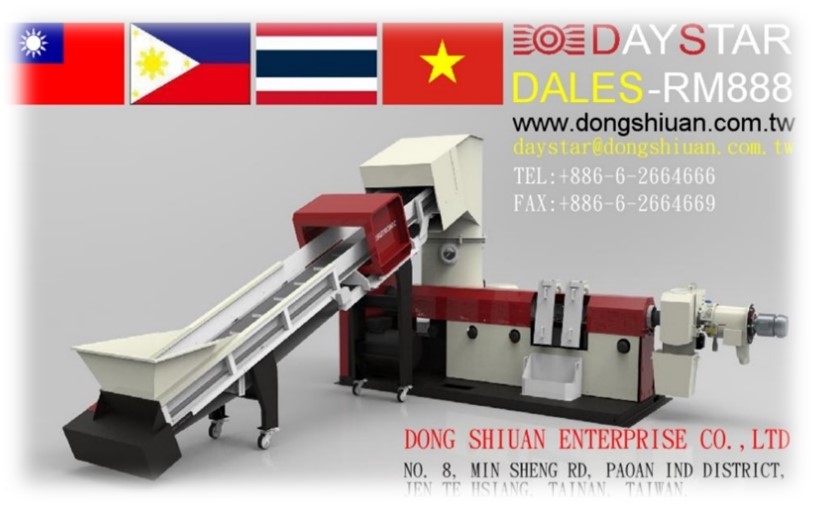
▲唐先企業自行研發的塑料回收製粒設備
但在塑料再生的生產作業過程中,當高達數百種的原料種類,對上十幾種的製程溫度、轉速參數,所面臨的是成千上萬種參數組合。以往都是依賴現場員工(老師傅的經驗)去調整各種生產製程條件。因此往往在轉換生產不同來料(如:PET、PP、PE)的過程中,會因為嘗試階段浪費掉不少原料。
傳統產業的專業資訊能力缺口
唐先企業知道數據資料的重要性,因此過去雖然有將製程參數紀錄下來,卻因為當時缺乏數據化的能力,主要以紙本形式,由現場的操作人員以人工操寫紀錄寫下來,累積了大量的紙本數據,但也因此缺乏具科學化且詳實的數據資訊可供即時參考與調整。
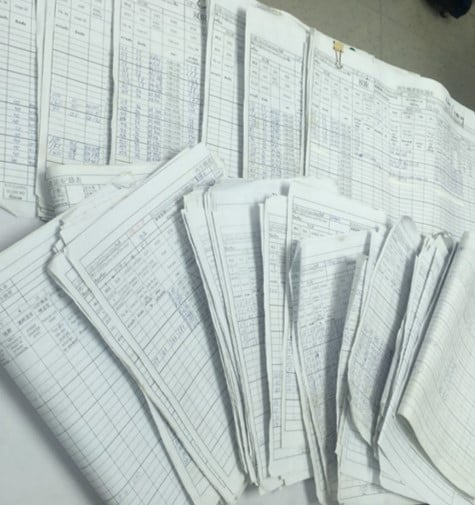
▲製程參數的手抄本,每小時記錄一次十幾種機器狀態與產量數字
在品管方面,也因為缺少產出的品質管制與單位時間產量的監控與反饋機制,導致實務上難以預測每一批的生產條件的獲利狀況,生管單位最後只能從結果去估計與平均攤提過程中的各種產能與成本的變化,無法客觀與即時地讓產線以最短的時間恢復合理的生產條件或當面對品質異常作出更明確的調整。
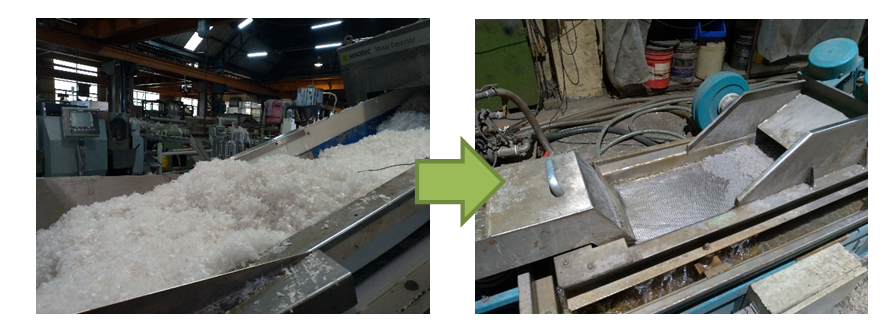
▲現場實況(左圖為回收碎料;右圖為造粒成品)
台灣廠商的機具製造能力十分堅強,許多現代化的機具已經具備了數據化功能,能夠將實時的狀態與資訊以物聯網的方式記錄下來。然而在工廠的現場與資訊系統的基礎建設是否已經準備好了呢?
當老師傅遇上AI
唐先企業透過政府相關單位引薦,與台灣資料科學公司媒合,共同攜手將導入AI服務與運用AI優化內部流程的構想與應用情境,先以廠內中型塑料再生產線作為試煉場域,建立成功標竿後,將此模式擴展至工廠內大型塑料回收再生機械設備上,持續驗證與應用。
首先雙方共同將過往之手抄紙本資料,以OCR輔以人工修正方式,將過去的參數資料數據化。唐先企業也與機具之人機介面廠商將操作面板以及參數數據導入之工廠之資料庫,使得能夠即時監控機具狀態,免除人工抄寫的繁複或錯誤性發生。
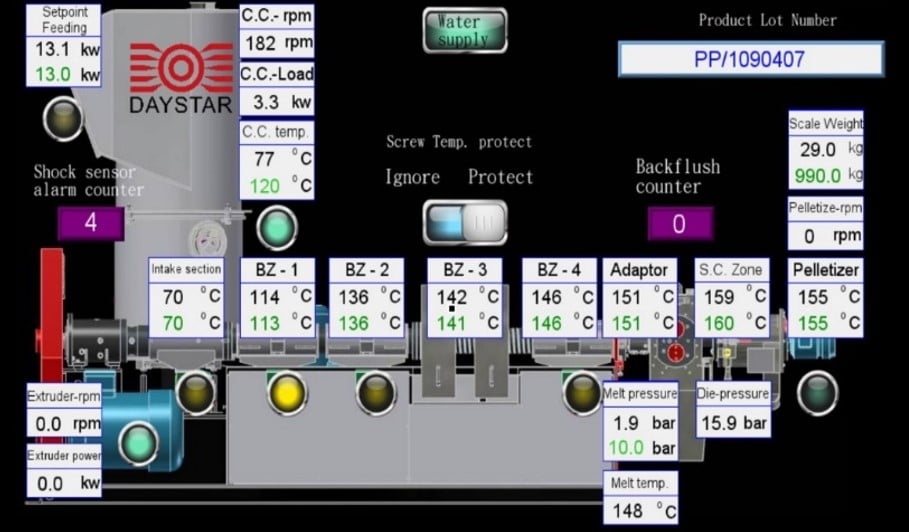
▲塑料回收再生造粒之機具面板,顯示當前各製程的溫度、轉速與使用電力的狀態
同時台灣資料科學公司再將數十種參數資料進行AI建模,透過情境分析,在環境參數與材料投入下模擬各種的產出可能性,找出關鍵特徵參數,並提供參數調整建議,降低試驗階段所需成本。
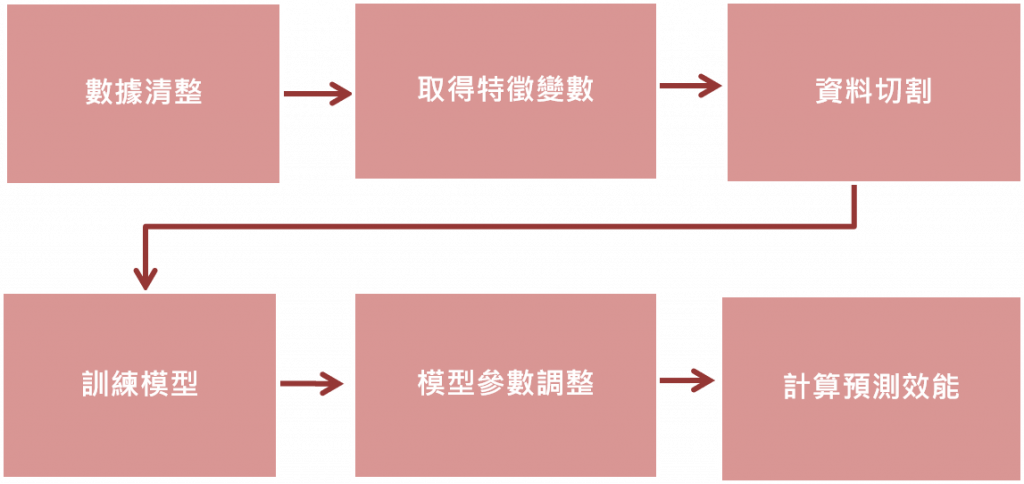
▲將數據分析應用於傳統產業機具製程中
當老師傅取得原物料之後,只需輸入相關料件特性參數,由系統自動生成建議的製程參數,再經由老師傅微調之後進行料件的試作,有效減少了錯誤嘗試所造成的料件、水費、電費以及人力的耗費。並且唐先企業更超前部屬,在塑料再生的製程上導入了「生產履歷」的概念,能夠透過掃描QRCode,取得該批產品的原料、製程等相關參數資料。
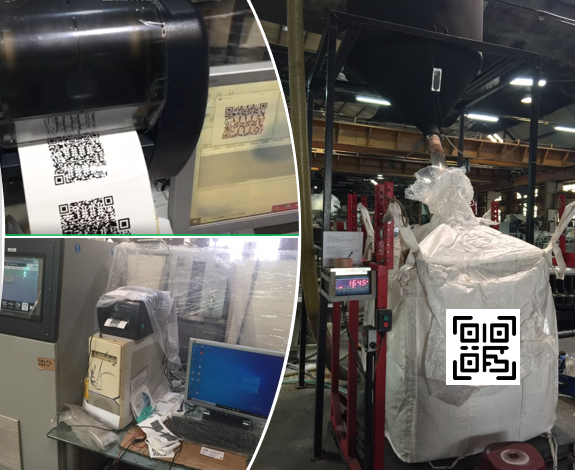
▲塑料再生造粒的產銷履歷
台灣中小企業機具實力堅強,只待「數據」的東風吹起
在工業2.0到3.0,甚至到4.0,許多台灣中小企業在轉型過程所面臨的問題,並非只是在機具升級上,而是把錢用在購入了現代化機具設備之後,產生了數據,卻不知道如何利用這些數據,若要這些廠商們自己培育一個專門的數據分析部門又顯得不太實際;在此同時的另外一面,台灣也有非常多軟體實力堅強的AI或數據分析的創新團隊,空有技術與實力,卻苦無場域與數據。因此若能夠充分的結合台灣傳統產業以及AI數據分析的創新團隊,除了能夠彌補現今傳統產業所面臨之人力與經驗傳承問題之外,也能夠讓台灣的AI發展與應用上往前跨進更大一步。